Pressure die casting manufacturers have the equipment and expertise to produce high-quality parts using the pressure die casting process. They may also have in-house design and engineering capabilities to assist customers with the design and development of their parts. In addition, pressure die casting manufacturers may offer additional services, such as assembly, finishing, and packaging, to help customers take their products from concept to completion.
Pressure die casting manufacturers can be found in a variety of industries, including automotive, aerospace, consumer products, and more. They may serve many customers, from large multinational corporations to small businesses, and produce various parts and components for multiple applications.
What is Pressure Die Casting?
Pressure die casting is a fast and reliable process for producing large quantities of parts that meet close dimensional tolerances. It is the most common type of die casting and involves injecting molten metal under high pressure into steel molds (tools). This solidifies rapidly (milliseconds to seconds) and is automatically extracted from the tool.
Types Of Pressure Die Casting
There are three main types of pressure die casting: low pressure, high pressure, and gravity die casting.
- Low-Pressure Die Casting
Low-pressure casting uses a crucible to fill a mold at a pressure of 0.7 bar to make rotationally symmetrical parts such as car wheels.
- High-Pressure Die Casting
High-pressure die casting is a metalworking process in which molten metal or metal alloy is injected into a mold at high pressure and speed. The resulting part has high precision, excellent surface finish, and mechanical properties.
- Gravity Die Casting
Gravity casting is a technique used to produce high-quality, dense castings with excellent mechanical properties. The process involves pouring molten metal directly from a ladle into a semi-solid or solid mold.
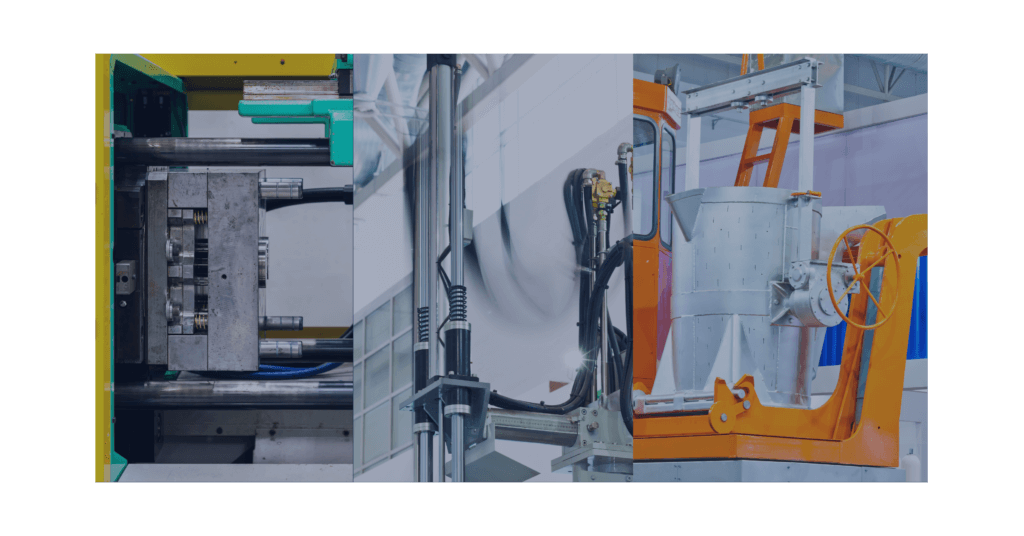
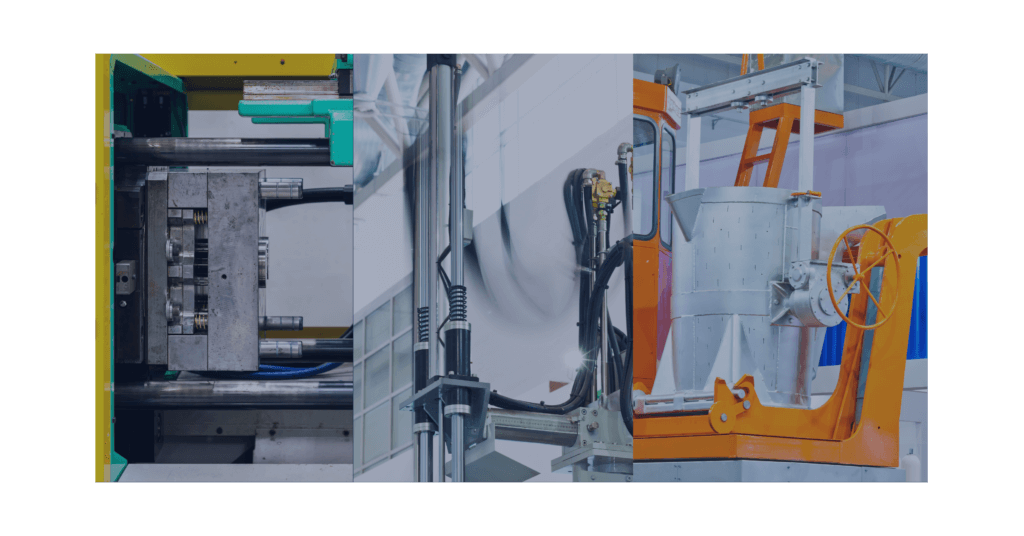
Pressure Die Casting Process
The pressure die casting process is a method in which molten metal is injected with high pressure into a mold cavity. The mold cavity is heated to a temperature that allows the molten metal to solidify and fill the cavity. After this occurs, the part is cooled and ejected from the mold.
The pressure die casting process results in castings with precise dimensional control and a good surface finish. Pressure die castings have thin walls, thanks to which they have less weight than sand castings and investment castings, as well as other metal casting methods. Additionally, they are economical to produce because they typically can be created before they need to be replaced.





Pros Of Pressure Die Casting
The economics of pressure die casting is well suited to producing large numbers of complex parts, mainly when replacement units must provide for in-service equipment. Pressure die castings offer dimensional control, good surface finish, thin walls, and/or reduced weight, all of which reduce the cost per part.
Cons Of Pressure Die Casting
Pressure die casting has several advantages over gravity die casting. It can produce more complex products requiring greater precision and fewer defects; it gives a better surface finish and achieves closer tolerances.
However, pressure die casting also has some disadvantages. Firstly, it requires complex and expensive equipment that is always maintained in good condition. Secondly, there is a significant capital investment needed for the setup. This means that pressure die casting is not suited to limited production runs or individual castings, which become proportionately more expensive the fewer of them there are.
Pressure die casting is also relatively inflexible compared to gravity die casting. Because it requires molten metal to be forced into the mold under pressure rather than being allowed to flow naturally and fill any voids that might exist in the mold cavity by its weight as gravity does.
Applications: Pressure Die Casting
Pressure die casting produces castings requiring a high degree of finish, particularly where relatively thin sections are involved. The technique is widely used to create car parts such as wheels, cylinder heads, and aerospace and automotive engine components. Other applications include kitchen equipment such as pressure cookers, cabinets for electronics applications, pump parts, and hydraulic components.
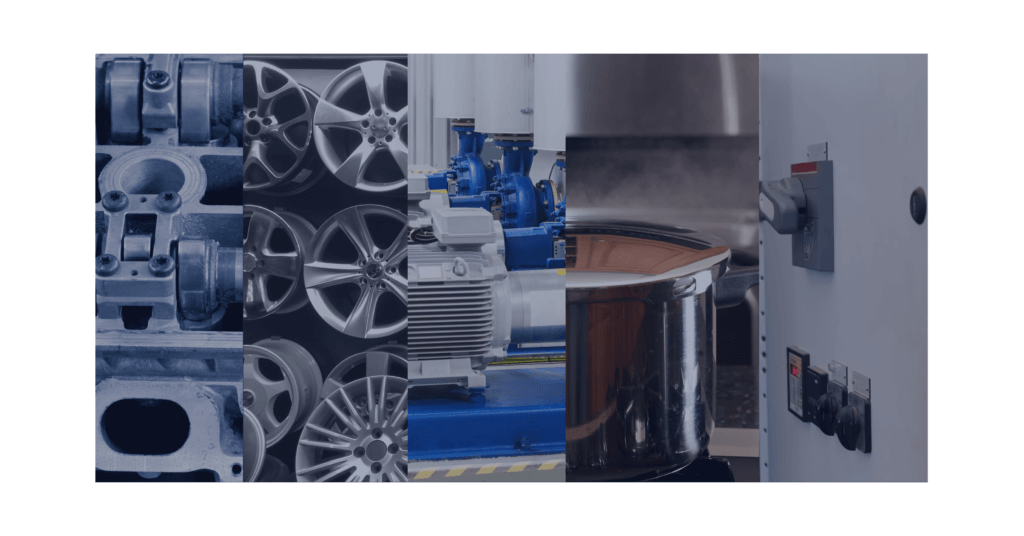
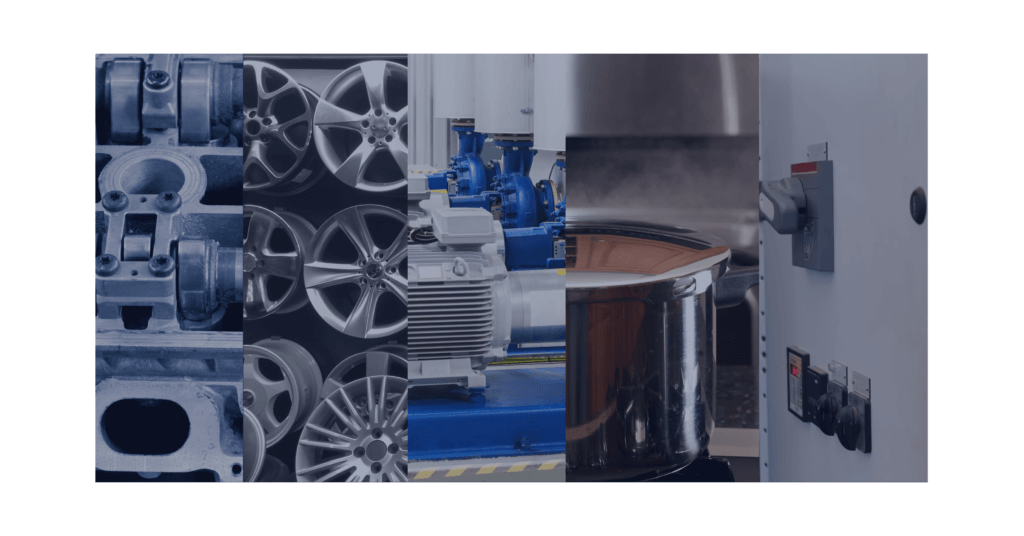
With industry experience, Zetwerk has a wide range of knowledge on the team and many ongoing client relationships. We understand how important it is to maintain control of every aspect of a new project. We work diligently to ensure your vision is maintained. This allows us to do much more than provide you with die castings for your product or project—we help bring your idea to fruition.
From prototype to production runs, Zetwerk’s pressure die casting manufacturing services are ideal for companies in the United States. Our experience in the industry means that we know the best approach to take for our clients, and we have a reputation to uphold from past projects.




