Materials Used in Investment Casting and their Properties
Investment casting is a manufacturing technique that has existed for millennia and is frequently employed today to produce high-precision metal components. This procedure involves using a wax pattern to create a mold that is coated with refractory material. The mold is then heated to remove the wax and harden the refractory material, leaving a void for the molten metal to fill. Investment casting utilizes various materials, each of which has qualities appropriate for specific uses.
The most frequently employed materials are stainless steel, aluminum alloys, titanium, and bronze. Due to its excellent corrosion resistance and superior mechanical qualities, stainless steel is a preferred choice for investment casting. It is frequently employed when the component is exposed to hostile conditions or corrosive substances.
In addition to its great dimensional precision and surface polish, investment stainless steel castings are ideal for applications requiring a smooth surface. Aluminum alloys are another prominent investment casting material. Due to their excellent strength-to-weight ratio, they are suited for aerospace and defense applications where weight is crucial. The corrosion resistance of aluminum investment castings makes them appropriate for usage in hostile situations.
Titanium is another common investment casting metal. This metal is renowned for its superior corrosion resistance, strength, and low weight. It is frequently utilized in medical and aeronautical applications due to its biocompatibility and tolerance to high temperatures. Bronze has been employed for thousands of years in investment casting. This metal is renowned for its superior corrosion resistance and high strength, making it perfect for use when the component is exposed to hostile environments or corrosive substances.
Additionally, bronze investment castings are renowned for their outstanding machinability and dimension stability. Investment casting is a versatile and accurate manufacturing technique that can generate high-quality metal components from various materials. Selecting a suitable material can have a substantial effect on the performance of the finished product. Investment casting can provide high-strength aircraft components, corrosion-resistant medical devices, and dimensionally correct tools.
Cost-Effective Investment Casting Solutions
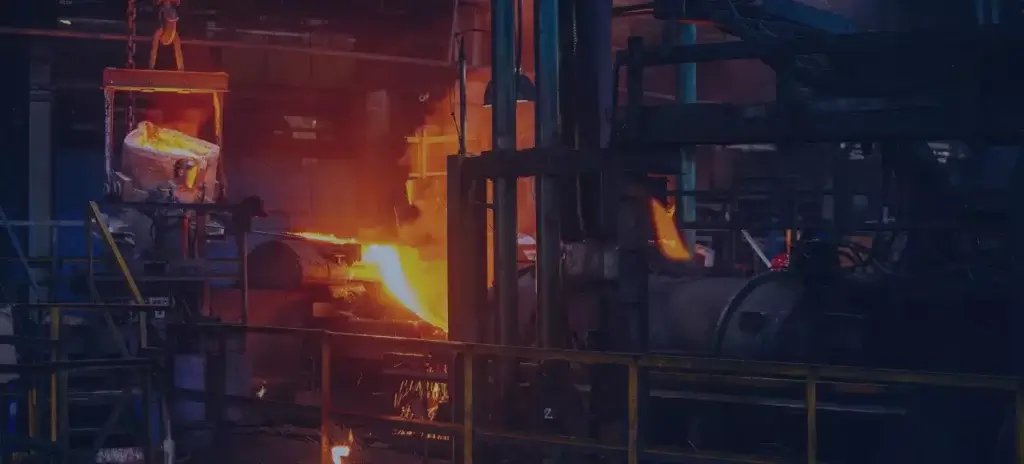
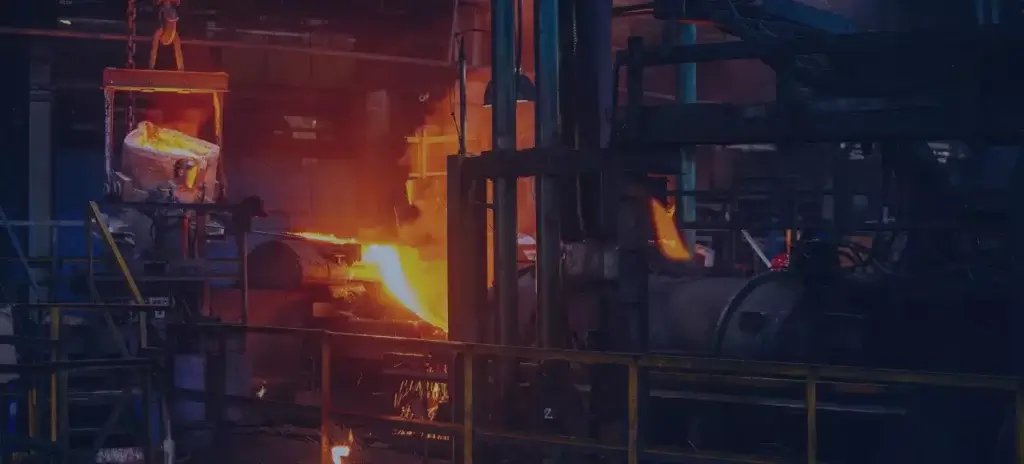
Investment casting has been a favored method for producing high-precision metal components for ages. However, it is sometimes viewed as an expensive process, which has prompted several businesses to investigate alternate techniques for manufacturing their components. Nonetheless, recent improvements in investment casting technology and the advent of cost-effective solutions have made investment casting more accessible to businesses of all sizes.
The utilization of digital technologies and automation is one of the primary contributors to the cost-effectiveness of investment casting. Using computer-aided design (CAD) and computer-aided manufacturing (CAM) tools, businesses may expedite their investment in casting operations and minimize the cost of producing high-quality parts. In addition, the automation of the investment casting process can cut labor costs and increase productivity.
Utilizing low-cost materials is a further cost-effective investment casting strategy. By adopting less expensive alloys or other materials, companies can dramatically cut the cost of making their parts while preserving the investment casting industry’s renowned precision and accuracy. For instance, aluminum alloys are typically a more economical alternative to more expensive metals such as titanium and stainless steel.
Additionally, investment casting can be made more cost-effective by lowering the number of manufacturing steps. By utilizing lost-wax investment casting, businesses can remove the requirement for machining or other secondary procedures, hence reducing the overall cost of creating the parts. In addition, by utilizing the most recent investment casting technology, businesses may make high-quality components with fewer flaws, hence decreasing the need for rework and further lowering costs.
The Future of Investment Casting in the Automotive Industry
The automotive sector is one of the world’s largest and most innovative industries. Investment casting has been an essential technology for making high-precision metal components for this industry for many years. However, the future of investment casting in the automotive sector is set to change due to the rapid growth of technology and the rising need for fuel-efficient and environmentally friendly automobiles. The increasing use of lightweight materials is one of the significant factors influencing the future of investment casting in the automobile sector.
To achieve fuel efficiency rules and reduce carbon emissions, automakers seek to lower the weight of their vehicles. By using lightweight materials in investment casting, such as aluminum alloys and titanium, automakers may reduce the weight of automobiles without compromising strength or durability. Increasing adoption of digital technologies is another trend that will shape the future of investment casting in the automobile industry. With the widespread use of computer-aided design (CAD) software and computer-aided manufacturing (CAM) technologies, investment casting companies can make high-quality components faster and more precisely than ever. In addition, by automating the investment casting process, businesses can minimize labor costs and increase the consistency of their parts.
The trend toward electric vehicles is also likely to impact investment casting’s future in the automobile industry significantly. Electric cars require lightweight, high-precision components that can endure the electric motors’ high power and torque. Investment casting is ideally suited to meet these requirements, and companies are anticipated to increase their usage of investment casting to manufacture electric vehicle components. The future of investment casting in the automobile sector is likely to be driven by trends such as the increased use of lightweight materials, digital technology, and electric vehicles. As technology progresses, investment casting will undoubtedly play a more prominent role in the automotive industry manufacturing of high-quality metal components.
Zetwerk is an industry-leading manufacturer that offers investment casting services for a variety of projects. Zetwerk can meet even the most complex investment casting requirements with our facilities and skilled staff. Our investment casting method entails the creation of molds from wax patterns, which are then utilized to make high-quality, complicated metal components with superior surface finishes.
Our investment casting services are appropriate for numerous industries, including aerospace, automotive, defense, and medical. We provide a selection of materials, including stainless steel, aluminum, and titanium. In addition, Zetwerk offers value-added services such as CNC machining and surface finishing to guarantee that the final product fits the exact specifications of the customer. Regardless of the project size, Zetwerk’s investment casting services can offer customers the needed, high-quality, and precise application components.



