High-pressure die casting is a process that uses high pressure to inject molten metal into a mold. The result is a part with high dimensional accuracy, a smooth surface finish, and good mechanical properties. The high pressure die casting process has been used by manufacturers of many products. Various high pressure die casting products in several industries, including engine blocks, cylinder heads, gears, wheels, and more. Here is a quick look at the High Pressure Die Casting process in simple terms and how the process works.
High Pressure Die Casting
High pressure die casting (HPDC) is an efficient, economical way to produce products with complex shapes. When a steel mold is made, a precision core is cast into the cavity of the die. The molten metal is then injected into this cavity within fractions of a second in an extremely high pressure environment to produce a product of nearly perfect quality. Molds are two-sided, one stationary and one moving.
A steel mold is mounted on plates of a die casting machine. Hydraulic pressure and pressurized gas move a piston forward to inject molten metal into a closed steel mold. The die casting machine has a clamping end that uses hydraulics and mechanical switches to absorb the pressure of molten metal as it fills a mold. It can take seconds for a ribbon-shaped part to be formed. It uses three metals such as zinc, aluminum, and magnesium.
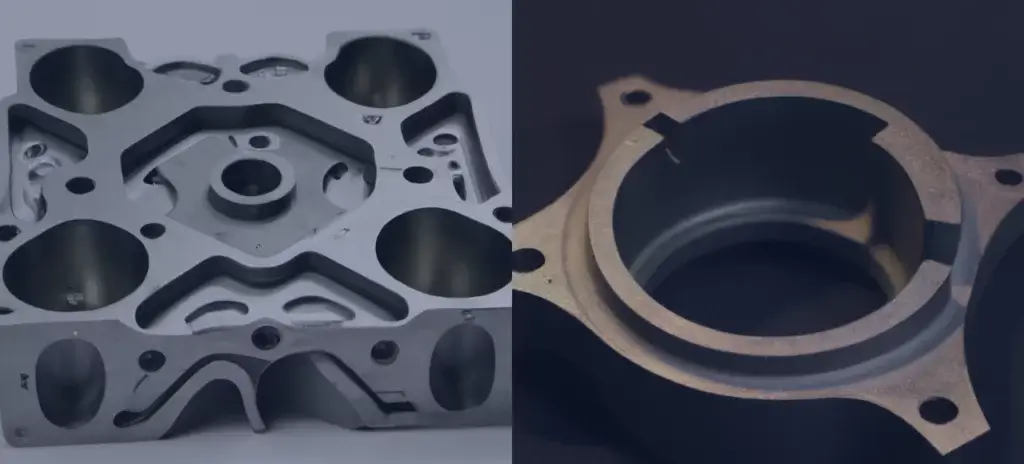
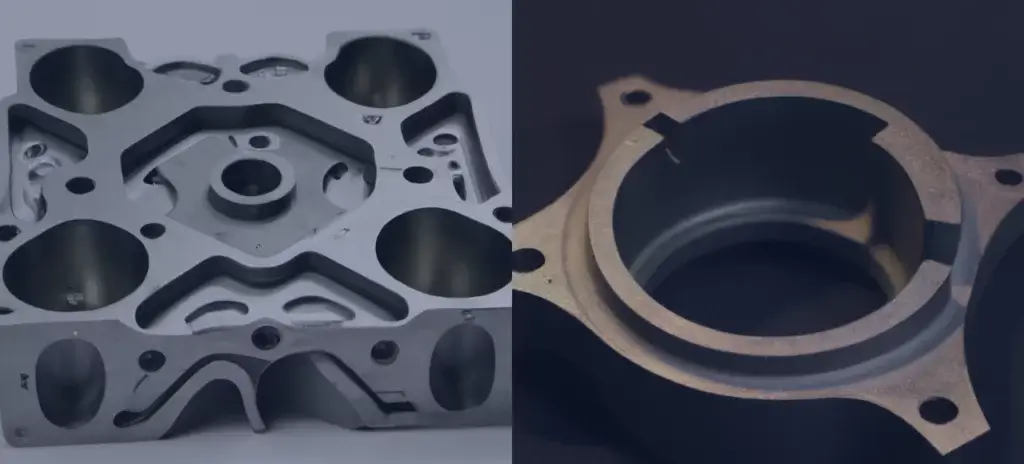
How Does High Pressure Die Casting Work?
High pressure die casting process involves four steps as follows:
- Mold Preparation : To begin high pressure die casting, a manufacturer first prepares the mold. To ensure that the metal parts fit together smoothly, the company first applies a lubricating coating to the inside of its molds.
- Injection : After the mold is prepared, molten metal is injected into it. The mold must be completely closed and sealed, or it cannot “accept” the metal under high pressure. The pressure range from 1,500 to 25,00 PSI (per square inch) used to inject molten metal into a mold can vary depending on the application. The mold maintains pressure until the metal has cooled and solidified.
- Aviation Industry : Due to the ability to create complex and intricate designs and the need for automation, this process is prevalent in the aerospace industry. Alloys of aluminum, zinc, and magnesium are used to manufacture aircraft engine components.
- Shakeout : When high pressure die casting is complete, the manufacturing company separates all the scrap from the newly formed cavity. The scrap is taken out of the form as it cools and hardens. This can cause excess scrap to remain in the cavity after solidifying, which must be removed before the mold can be used again.
- Medical Industry : High pressure die casting makes high-quality surgical instruments and other medical devices. HPDC is also used to produce imaging equipment, infusion pumps, and many other products.
- Cavity Ejection : Manufacturers then push the newly created cavity out of the mold. The ejector pins in the mold push out the cavities when engaged; this usually happens after cooling. Of course, the cavities must be strong enough to withstand being pushed out. If there are still liquid metal blanks inside, manufacturers must wait for them to cool before pushing them out of the mold.
- Automobile Industry : High pressure die casting can create a range of aluminum and magnesium automotive structural components. It manufactures parts such as gearboxes, engine blocks, engine mounts, oil pans, and structural cross elements.
- High Pressure Die Casting Products In Industries : High pressure die casting products are used in many industries because of their superior quality.
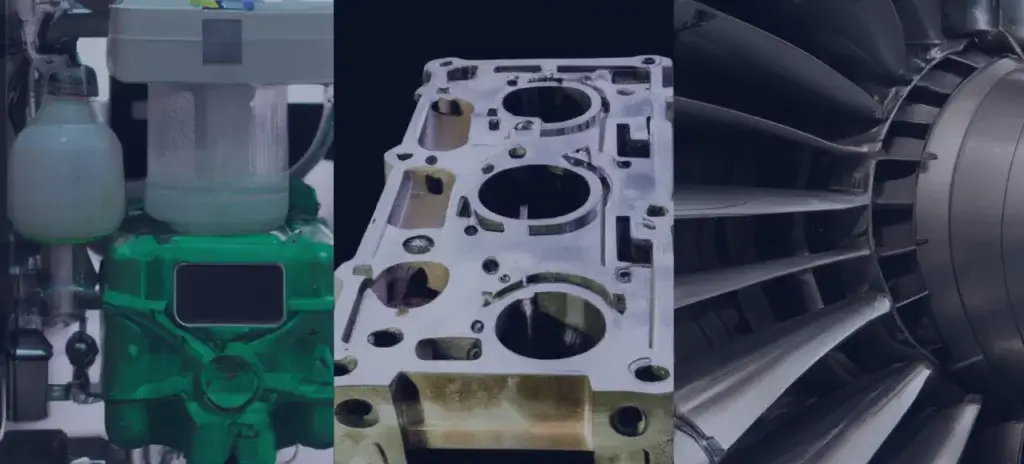
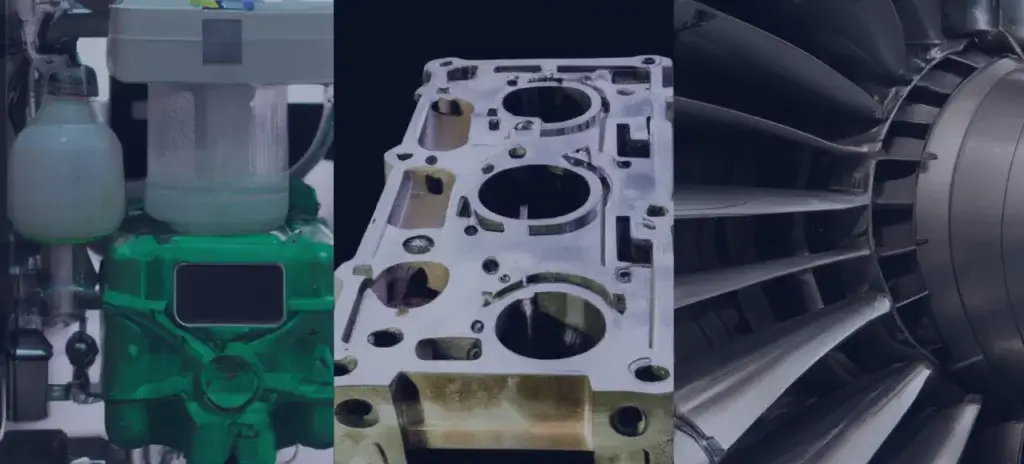
Advantages Of High Pressure Die Casting
Die casting can efficiently make massive, lightweight metal parts in huge quantities. Additionally, the HPDC method yields components with exceptional surface polish, outstanding homogeneity, and ideal mechanical qualities. Due to its superior dimensional precision and clean surfaces, HPDC generally requires minimal machining. High pressure die casting is a cost-effective and time-saving manufacturing method that:
- Produce robust, lightweight components that require less machining than finished components.
- Create elaborate and intricate one-piece shapes without welding or assembly.
- It offers a greater variety of forms than other metal manufacturing methods.
- Obtain close tolerances
For manufacturers, the advantages are clear: reduced scrap and improved productivity. That’s to say nothing of the flexibility in material choices and design. If you’re looking to speed up your manufacturing process, provide intricate and customizable parts, and reduce equipment costs, high pressure die casting could be the solution you’re looking for.
Despite the initial investment in equipment and molds, the cost savings from reduced scrap and improved productivity make high pressure die casting an attractive option for manufacturers. With advancements in technology and materials, the possibilities for high pressure die casting are only increasing.
Zetwerk is a leading high pressure die casting manufacturer, offering an extensive range of products for various industries. With decades of experience in the trade, Zetwerk has built a comprehensive portfolio of high pressure die casting products, ranging from simple and complicated components to large-scale structures. Utilizing advanced technology and cutting-edge materials, Zetwerk’s team strives to provide quality products that are both durable and cost-effective. By directly controlling the entire production process from design to delivery, Zetwerk ensures customer satisfaction with every order.



