Discovering the Latest Developments in High Pressure Die Casting Industry
High Pressure Die Casting (HPDC) technology has been an essential part of the manufacturing industry for several decades. Over the years, many advancements and innovations have been made to improve this process’s speed, accuracy, and efficiency. These improvements have significantly impacted the production of high-quality metal components and have made HPDC a popular choice for many industries, including automotive, aerospace, and electronics. One major development in HPDC technology has been the integration of computer-aided design (CAD) and simulation. This allows manufacturers to design and test parts virtually, reducing the need for prototypes and time-to-market. The use of simulation software also enables engineers to optimize the casting process, including the mold’s design and the molten metal flow, resulting in higher quality components and reduced scrap rates.
Another significant innovation in High Pressure Die Casting is the use of multi-cavity tooling. This involves the creation of multiple cavities within a single mold, allowing for the simultaneous production of various parts in a single cycle. This dramatically increases production efficiency and reduces the overall cost of manufacturing. Multi-cavity tooling is also beneficial for high volume production, as it reduces the time required for tool changes and enables manufacturers to meet the high demands of their customers. Real-time monitoring and control have also become crucial for high pressure die casting. Advanced sensors and monitoring systems are used to track the molten metal’s temperature, pressure, and flow during the casting process. This enables engineers to make real-time adjustments to the process to maintain the quality and consistency of the final product.
In recent years, high pressure die casting companies have also made significant efforts to improve the sustainability of their operations. Energy consumption is a primary concern, and many companies have adopted energy-efficient systems and processes to reduce their carbon footprint. For example, some companies have adopted low-pressure casting, which consumes less energy compared to traditional high-pressure casting. The advancements and innovations in technology have greatly improved the casting process’s speed, accuracy, and efficiency. These developments have also enabled manufacturers to produce high-quality components with reduced lead times and reduced costs. As the demand for high-quality metal components continues to grow, further innovations will likely be made, further improving the process and making it an even more popular choice for manufacturers worldwide.
Why choose high pressure die casting companies for custom projects
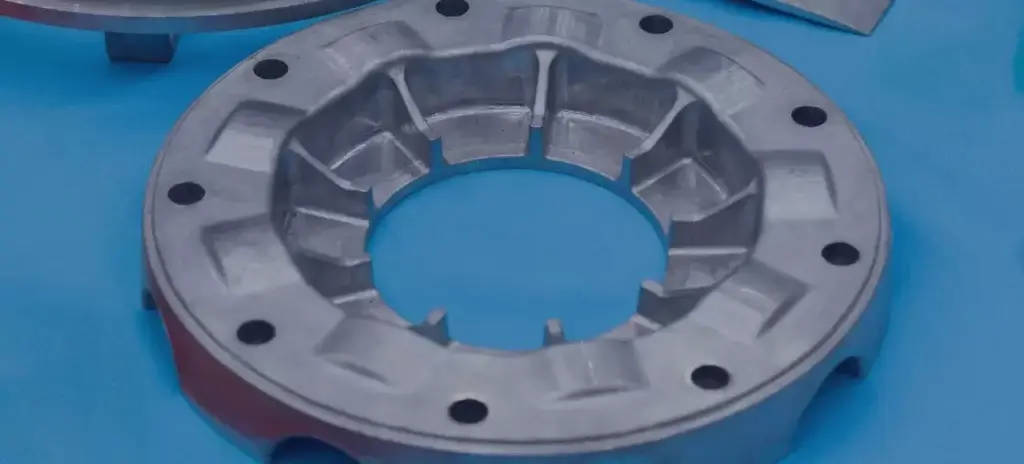
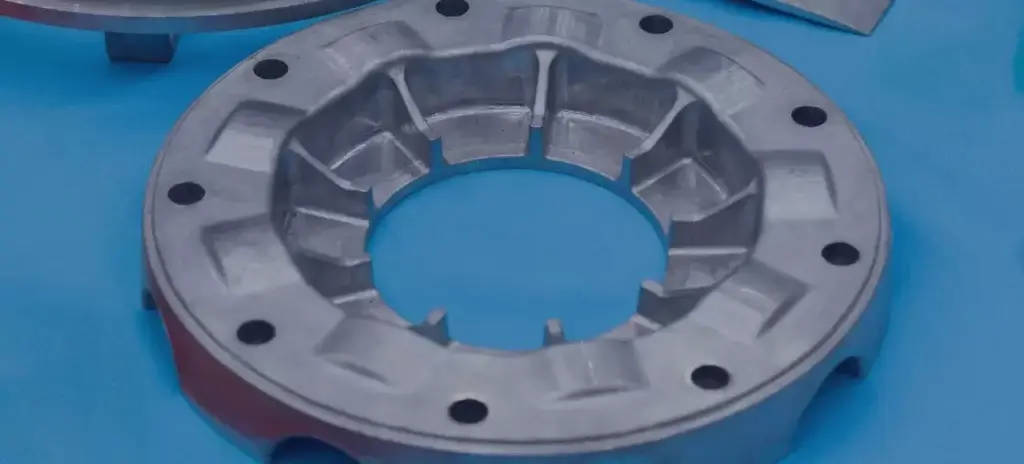
High Pressure Die Casting (HPDC) is a process that offers a cost-effective and efficient alternative for unique projects needing metal components with exact details and tight tolerances. Working with a reputable HPDC company can provide organizations with numerous benefits. The rapid and accurate manufacture of high-quality components is one such advantage. Companies specializing in high pressure die casting use cutting-edge technology and processes to eliminate waste and produce high-precision parts with strict deadlines or large production volume requirements. Another advantage is the capacity to manufacture intricately detailed complex pieces. High pressure die casting allows for casting parts with fine details and strict tolerances, making it excellent for applications with intricate shapes and designs. This level of accuracy ensures that the final output meets the project’s requirements.
Additionally, cost-effectiveness contributes to high pressure die casting’s popularity in custom projects. Also, renowned for its cheap unit cost and excellent production efficiency, making it attractive to organizations that manufacture large quantities of high-quality components. Companies specializing in high pressure die casting know how to improve the casting process by minimizing waste and optimizing productivity, resulting in a cheaper overall project cost. Materially speaking, businesses are adaptable and versatile in the die casting industry. They can cast a variety of metals, including aluminum, zinc, and magnesium, allowing firms to select the most appropriate material for a specific project. This adaptability enables businesses to produce components for numerous aerospace, automotive, and electronics industries.
Companies in the high pressure die casting industry have a reputation for supplying high-quality components that fulfill customer specifications and requirements. In addition, they give unmatched customer service and support, ensuring that businesses receive the assistance necessary to accomplish their projects. Selecting a reputable company for custom projects offers numerous advantages, such as rapid and efficient production of high-quality components, the ability to create complex parts with intricate details, cost-effectiveness, material flexibility, a track record of delivering quality components, and superior customer service.





Maximizing Your Custom Project Potential with High Pressure Die Casting
High Pressure Die Casting (HPDC) is a well-known technology for making custom metal parts, and its many advantages make it an attractive alternative for enterprises. Here are a few benefits of utilizing high pressure die casting for unique projects:
- Precision and accuracy: The process gives precise control over the casting process, enabling the production of high-quality components with tight tolerances and intricate details. This precision ensures that the final product meets project specifications and requirements.
- Fast production: Companies use state-of-the-art technology and procedures to minimize waste and produce high-precision parts with tight deadlines or high production volume needs. This results in faster production times and increased efficiency.
- Cost-effectiveness: High pressure die casting is known for its low unit cost and high production efficiency, appealing to businesses that must produce large volumes of high-quality components. Companies have the expertise to optimize the casting process, reducing waste and maximizing efficiency, resulting in a lower overall project cost.
- Quality assurance: Working with a reputable High pressure die casting company offers peace of mind and assurance in the quality of the final product. Companies are renowned for delivering high-quality components that meet customer requirements and specifications.
- Material versatility: Companies are flexible and versatile in terms of materials. They can cast various metals, including aluminum, zinc, and magnesium, enabling businesses to choose the best material for their particular project.
The benefits of using high pressure die casting for custom projects include precise and accurate parts, fast production times, cost-effectiveness, material versatility, and quality assurance. These benefits make HPDC an attractive option for businesses that need to produce high-quality metal components quickly and efficiently. Zetwerk’s high pressure die casting process is designed to meet the highest standards of accuracy and precision, allowing us to produce complex shapes and designs efficiently. We ensure that every project is completed to the highest standard, focusing on efficiency, cost-effectiveness, and customer satisfaction. With our commitment to excellence, Zetwerk is the ideal partner for businesses looking to achieve their manufacturing goals in high pressure die casting.




