Unlocking the Power of Customization: The Vital Role of Gravity Die Casting Manufacturers
Gravity die casting manufacturers play a significant role in the development of client-specific solutions. The producers have considerable experience and knowledge of the gravity die casting process and are equipped with cutting-edge technology and equipment to make high-quality castings. Manufacturers work closely with clients to comprehend their unique design requirements and specifications and then supply custom-tailored solutions. One of the primary roles of producers of gravity die casting is to give clients technical support throughout the entire process, from initial design to final production. This involves offering advice on material selection, preserving the integrity of the design, and ensuring that the final product satisfies all required quality and safety standards.
In addition, gravity die casting manufacturers can do development, testing, and sample manufacturing, allowing customers to confirm the design and functionality of their products before mass production. This reduces the likelihood of production problems and guarantees that the finished product fulfills the client’s requirements. Moreover, gravity die casting manufacturers can scale production to meet clients’ needs, whether they require little or huge quantities. Additionally, they can offer varying lead times to ensure customers receive their items on the schedule. Overall, gravity die casting manufacturers play a crucial role in the development of bespoke client solutions. Their expertise and experience in the industry, together with their advanced technology and tools, enable them to supply clients with the highest quality casting products that fit their individual needs and specifications.
Step-by-Step procedure of Gravity Die Casting
Gravity die casting is a standard metal casting technique that fills a mold with molten metal using gravity. The procedure requires using a two-part metal mold, also known as a die, to produce the finished component’s required shape. Gravity die casting can be split down into the following stages:
- Mold Design and Preparation: The first step in gravity die casting is the design and preparation of the mold. Typically, the mold consists of two components that generate a cavity in the desired component’s shape. The mold is created using computer-aided design (CAD) software and high-precision manufacturing techniques.
- Heating the Die: After the mold has been prepared, it is heated to a temperature appropriate for casting. The temperature of the die must be carefully regulated to prevent flaws such as shrinkage and cracking in the final product. Typically, the die is heated by electrical or gas-fired heat sources.
- Cooling and Solidification: After the molten metal has been poured into the mold, it is cooled and solidified. The cooling procedure is crucial and must be precisely managed to enable the production of a defect-free, homogeneous component.
- Inspection and Testing: The final step of the gravity die casting process is the inspection and testing of the component to confirm that it meets the required specifications. Visual and dimensional inspection techniques and non-destructive testing procedures are commonly used to inspect the part.
- Pouring the Molten Metal: The molten metal is poured into the desired mold and allowed to cool and harden. Gravity draws the molten metal into the mold, filling it and producing a component with exceptional precision and accuracy. Gravity die casting can utilize a variety of metals, including aluminum, magnesium, and zinc alloys.
- Removal of the Component: The die is opened after the metal is cooled and solidified, and the component is extracted. To attain the desired finish, the part may require extra processing, such as trimming or sanding.
Gravity die casting is a complex process that demands meticulous attention to detail and perfect control of multiple variables, such as temperature, pressure, and flow rate. Typically, the procedure is mechanized, which ensures consistent quality and efficiency. The use of specialist equipment and the requirement for constant monitoring of the process can increase the cost of gravity die casting. However, the high precision and accuracy of the final component frequently make it appropriate for a wide variety of applications.





Gravity Die Casting Industry: The Impact of New Materials and Technology
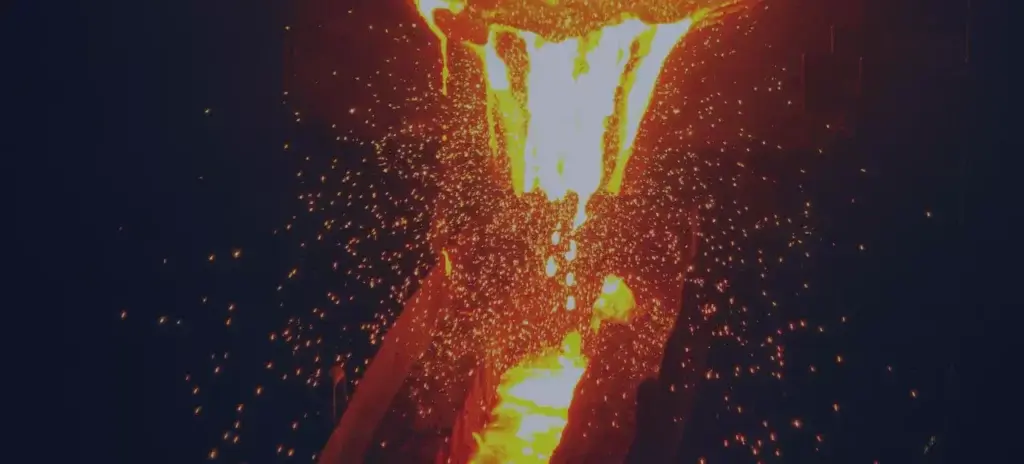
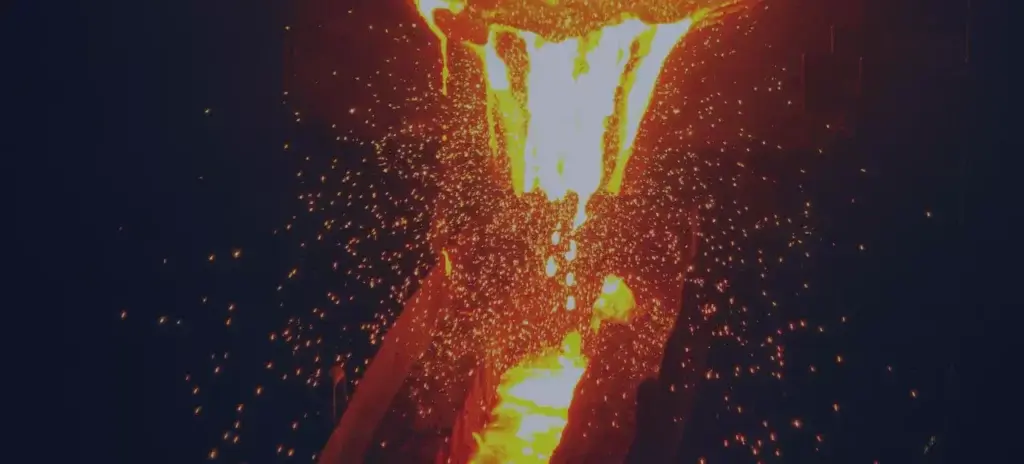
In recent years, the gravity die casting industry has benefited from developing new materials and introducing innovative technology. These innovations have significantly impacted the industry and enabled producers to overcome several previously encountered obstacles. Nonetheless, new obstacles have surfaced, and manufacturers must continue to adapt in order to remain competitive. The development of novel materials has been one of the most significant industry developments. The use of lighter and more durable materials has enabled manufacturers to build components that are more resilient and able to resist more substantial amounts of stress. This has increased gravity die casting in areas where high-performance components are needed, such as aerospace, automotive, and medicine. The subject of simulation and modeling is another area where new technology has had a substantial impact. Producers can mimic the entire casting process and optimize the component’s design using computer-aided design (CAD) and computer-aided engineering (CAE) technologies. This has resulted in a reduction in the number of iterations required to generate the final component, hence reducing lead times and enhancing productivity.
Advanced sensors and control systems have also significantly influenced the growth of the gravity die casting business. These technologies provide real-time data on the casting process and enable producers to make real-time adjustments, thereby decreasing the chance of defects and enhancing product quality. In addition, the introduction of automation and robotics has boosted the casting process’s speed and efficiency, reduced the need for manual labor and shortened lead times. Despite these developments, new obstacles have surfaced. Reducing emissions and increasing energy efficiency are the industry’s greatest issues. Using high temperatures and high energy inputs during the casting process has increased energy consumption and emissions, necessitating the adoption of more sustainable methods by manufacturers. Maintaining the finished component’s high quality while lowering lead times and prices is a further obstacle. Due to rising competition and the requirement to create components more quickly and at lower costs, manufacturers must develop ways to strike a balance between quality, speed, and cost efficiency. The new materials and technological improvements have substantially impacted the gravity die casting business. Utilizing these innovations, manufacturers can overcome industrial constraints and produce high-quality components more quickly and efficiently. Nonetheless, new obstacles have surfaced, and manufacturers must continue to adapt in order to remain competitive.
When it comes to gravity die casting, Zetwerk’s expertise and advanced technologies make them the go-to solution for any industry looking to enhance their production capabilities. At Zetwerk, we understand that every industry has its unique requirements and challenges, and that’s why we work closely with clients to deliver tailor-made solutions that meet their specific needs. Our expert team uses the latest technologies and techniques to ensure the highest level of precision and quality in every project we undertake.




