Raw Material Price Fluctuations: The Uncertainty that Impacts the Cost of Die Casting
Die casting is susceptible to having its price altered significantly by several factors, one of which is the cost of the raw materials. Die casting uses a variety of raw materials, some of which are subject to market fluctuations, such as aluminum, zinc, and other metals. These changes in the market can have a direct impact on the overall cost of manufacturing. Many things can affect the prices of these essential commodities. These things include supply and demand, natural disasters, and geopolitical tensions. Consequently, shifts in the prices of raw materials have the potential to have a sizable effect on the ultimate cost of die-cast parts. For instance, aluminum is a metal that is frequently used in the process of die casting. Because aluminum has such a wide range of applications, particularly in the transportation and construction industries, its price fluctuates frequently. Die casting is susceptible to experiencing a considerable cost increase in the event that there is a rapid rise in the price of aluminum. This is because aluminum accounts for a significant amount of the overall manufacturing cost. This, in turn, can affect the competitiveness of die casting in the market because the increase in price may cause die casting to be more expensive compared to other manufacturing methods.
Zinc is yet another metal that is frequently utilized in the process of die casting and is similarly susceptible to price changes. The price of zinc can be affected by various factors, including shifts in the demand for galvanized steel and fluctuations in the amount of zinc that can be mined and refined. Die casting may see a proportional increase in its cost in response to an increase in the price of zinc, turning out finished products that are both more expensive and less competitive in the market. Die casting pricing can be affected by a variety of factors, including the cost of energy sources, such as the price of electricity and natural gas. Energy is an essential component of the die casting process since it is essential for melting the metal and keeping the temperature of the casting process at a consistent level. Die casting may lose some of its market competitiveness if there is a sudden spike in the cost of energy, leading to a general rise in production costs and raising the price of die casting.
The cost of the raw materials required for die casting is an essential consideration that can play a considerable role in determining total expenditures. Die casting manufacturers must keep a close eye on the prices of various metals, such as aluminum and zinc, as well as energy costs, as these prices are prone to swings. As a result, it is imperative that die casting manufacturers closely monitor these prices and make adjustments to their production processes as required. It will be essential for the competitiveness and success of die casting in the market to have the ability to manage the influence of the prices of raw materials on the costs of producing die cast parts.
Optimizing Die Casting: How Automation is Driving Down Costs
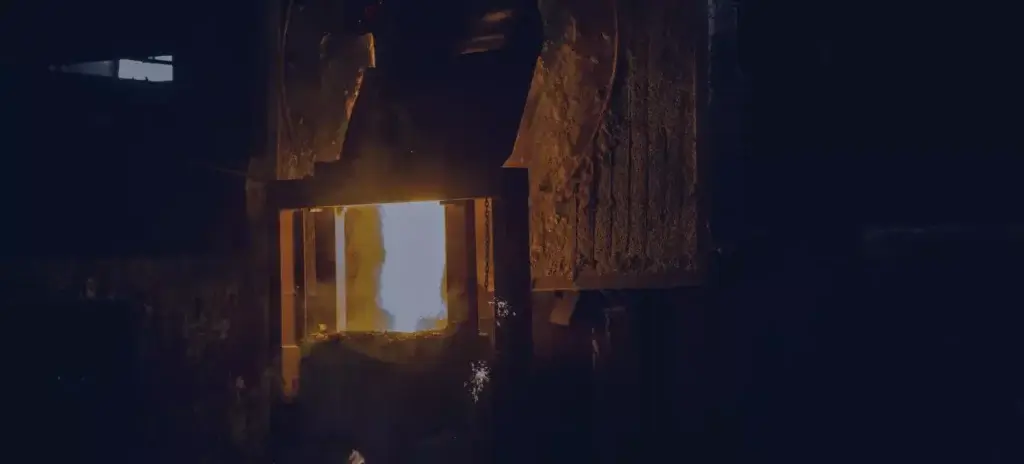
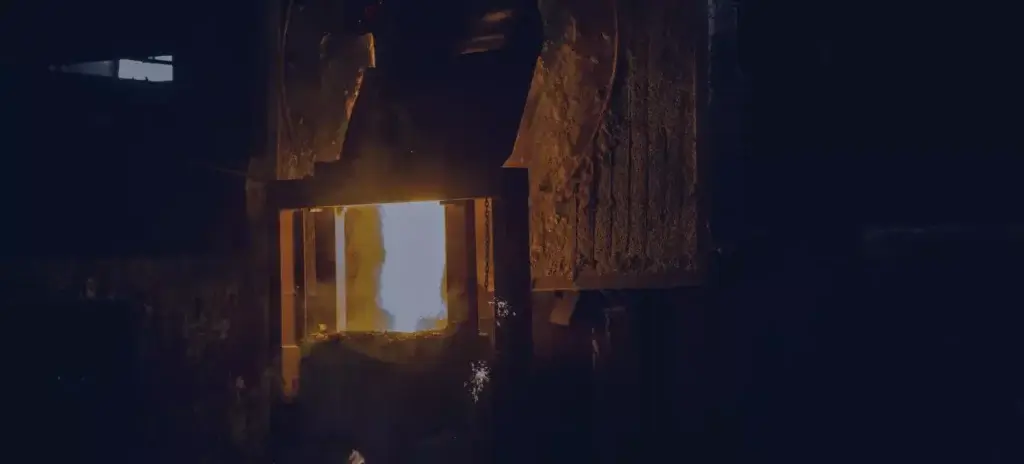
The importance of automation in the industrial business, including the die casting industry, has increased. Automation may improve the effectiveness of production processes and reduce costs, making it a crucial component of die casting production. In this regard, automation can significantly reduce the cost of die casting and increase its market competitiveness. Automation can lower die casting costs by reducing the staffing necessary in the production process. Automated casting machines can significantly minimize the requirement for manual labor in the casting process, enabling businesses to produce parts with improved consistency and efficiency. Automatic casting machines can also be programmed to improve the casting procedure, thereby minimizing waste and enhancing product quality. In addition to reducing labor expenses, automation can also minimize the energy costs associated with the die casting process. Automated casting machines can be built to run more efficiently and consume less energy, hence lowering production costs and enhancing profitability. Additionally, energy efficiency can assist in lessening the environmental impact of die casting, making it a more sustainable manufacturing process.
Automation can also cut the price of raw materials used in die casting. For instance, automated casting machines can be set to regulate the amount of raw material utilized during each casting cycle, minimizing waste and increasing productivity. This can result in substantial cost reductions, particularly for costly raw materials such as aluminum and zinc. Utilizing robots for post-casting processing is another method by which automation can minimize die casting costs. Robots can be taught to do activities like deburring, trimming, and polishing, thereby eliminating the need for manual labor and enhancing the speed and consistency of these processes. Additionally, automated robots can function around the clock, reducing downtime and maximizing production process efficiency. Automation plays an increasingly vital role in the die casting sector, aiding producers in lowering costs and enhancing their goods’ market competitiveness. Automation can dramatically reduce the cost of die casting and make it a more cost-effective manufacturing process by reducing labor expenses and increasing the efficiency of raw material utilization.
Zetwerk is a leading manufacturing company specializing in die casting for custom projects tailored to meet the individual industry needs of our clients. With the right experience and expertise in the industry, Zetwerk provides top-notch die casting services that are unparalleled in terms of quality, precision, and efficiency. What sets Zetwerk apart is our commitment to providing the best pricing to our customers, ensuring that they receive the most cost-effective solutions without compromising on quality. Whether it’s a small or large-scale project, Zetwerk is equipped to handle it all and deliver exceptional results.



