There are several reputable die casting companies in the United States. However, only a handful – like Zetwerk – are known for their exceptional quality products, dependable delivery, and superb customer service.
It’s essential to do your research to compare and find the best die cast manufacturer that fits your needs and budget. You’ll want to consider their experience, capabilities, quality control processes, and pricing.
By considering these factors, you’re more likely to find a die casting company that will meet (and exceed) your expectations. Consider factors such as location, turnaround time, and the types of materials and processes they offer.
What is Die Casting?
Die casting is a process used to create metal parts. Molten metal gets injected under high pressure into a mold cavity, also known as a die. The mold is usually made of steel or aluminum and is precision-machined to produce the desired shape of the final product. Die casting is typically used to create a wide range of metal parts, including car parts, aerospace components, electrical connectors, and various mechanical components.
Die Casting Process – Types
There are several types of die casting, including:
- Hot chamber die casting
- Cold chamber die casting
In hot-chamber die casting, the molten metal is injected into the mold under pressure through a plunger or a gooseneck. This process is typically used with metals that have low melting points, such as zinc and magnesium.
In cold-chamber die casting, the molten metal is poured into a chamber, and a piston injects the metal into the mold under high pressure. This process is typically used with metals with higher melting points, such as aluminum and copper.
Die casting is a fast and efficient process that can produce high-quality parts with good dimensional accuracy and surface finish. It is also relatively inexpensive, making it a popular choice for mass-producing metal parts.
Steps Involved in Die Casting Process
The die casting process involves several steps: clamping, injection, cooling, ejection, and trimming.
- Clamping: The first step in the die casting process is clamping the mold halves together. The mold consists of two halves that are held in place by a clamping force provided by the die casting machine.
- Injection: The molten metal is then injected into the mold cavity under high pressure. This step is typically done using a hydraulic or mechanical press.
- Cooling: After the molten metal has been injected into the mold, it begins to cool and solidify. The mold’s cooling process is typically assisted by water or air cooling channels.
- Ejection: Once the metal has solidified, the mold is opened, and the finished part is ejected. This is typically done using a spring-loaded ejector pin or a hydraulic cylinder.
- Trimming: After the part has been ejected, any excess material, such as flash or runners, is trimmed off. This is typically done using a trimming die or a CNC machine.
After these steps are completed, the finished die cast parts are typically inspected for quality and surface finish. They may require additional finishing steps, such as deburring or polishing before they are ready for use.







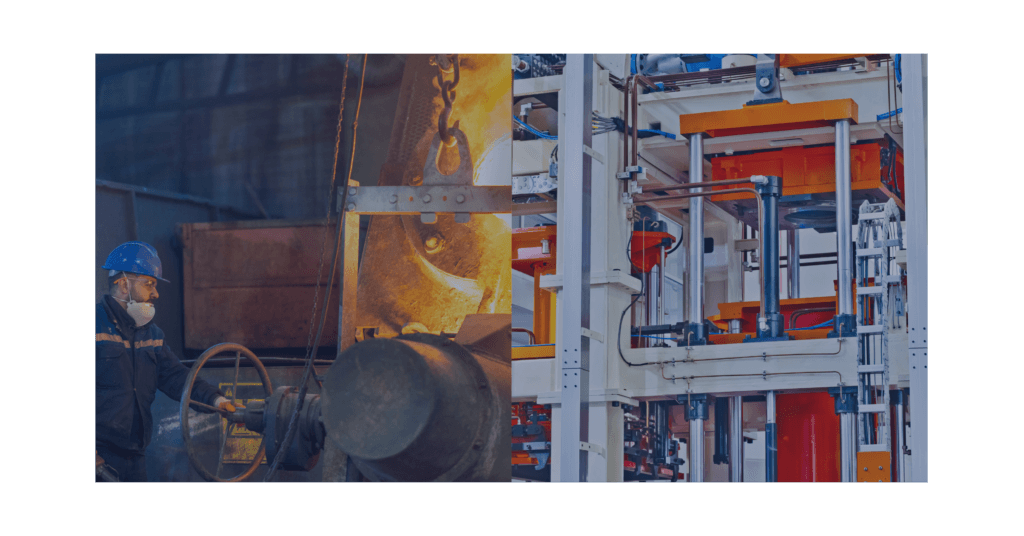
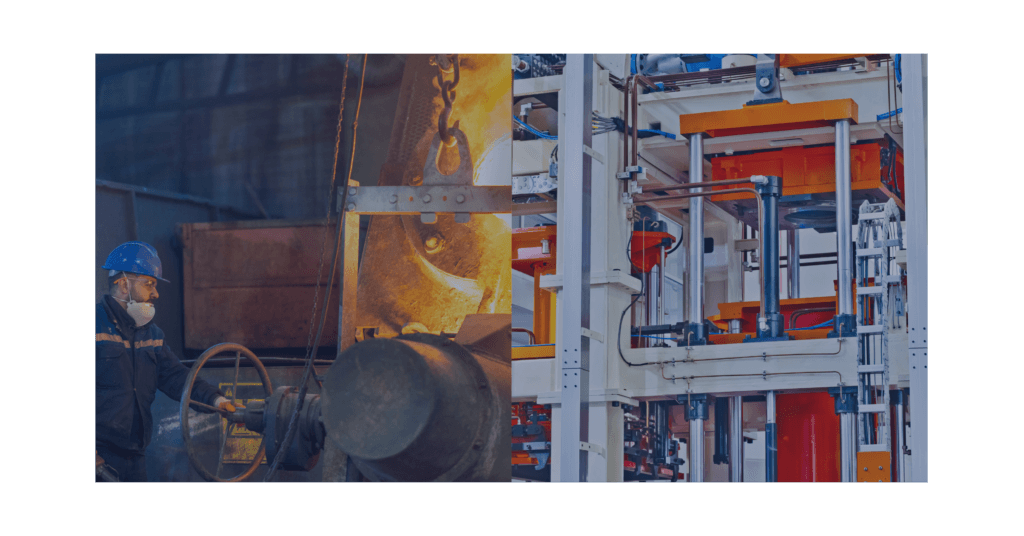
Die Casting Applications
Casting is a metal forming process that can produce precision parts with a smooth surface finish. It’s used to create a range of metal parts, including gears, handles, brackets, and structural components. It’s also used to manufacture automotive, aerospace, and electronics parts.
Some typical applications of die casting include:
- Automotive parts: Die casting produces a wide range of automotive parts, including engine blocks, cylinder heads, transmission housings, and brake calipers.
- Aerospace parts: Die casting produces structural components for aircraft, such as wing ribs, fuselage frames, and landing gear components.
- Electronics: Die casting produces housings and other components for electronic devices, such as smartphones, computers, and appliances.
- Medical devices: Die casting produces many medical devices, including implantable devices, surgical instruments, and diagnostic equipment.
- Consumer goods: Die casting produces a wide range of consumer goods, including toys, sporting goods, and household products.







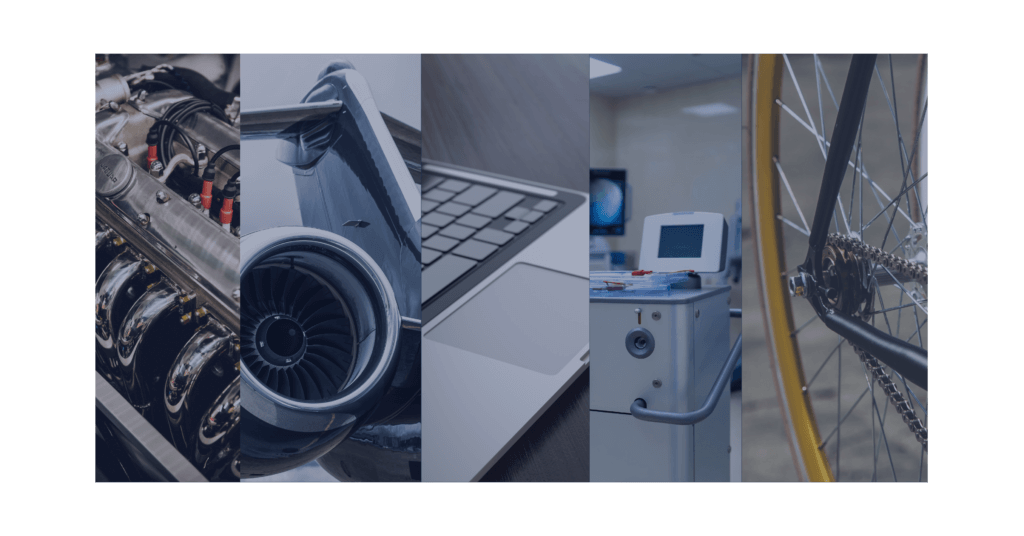
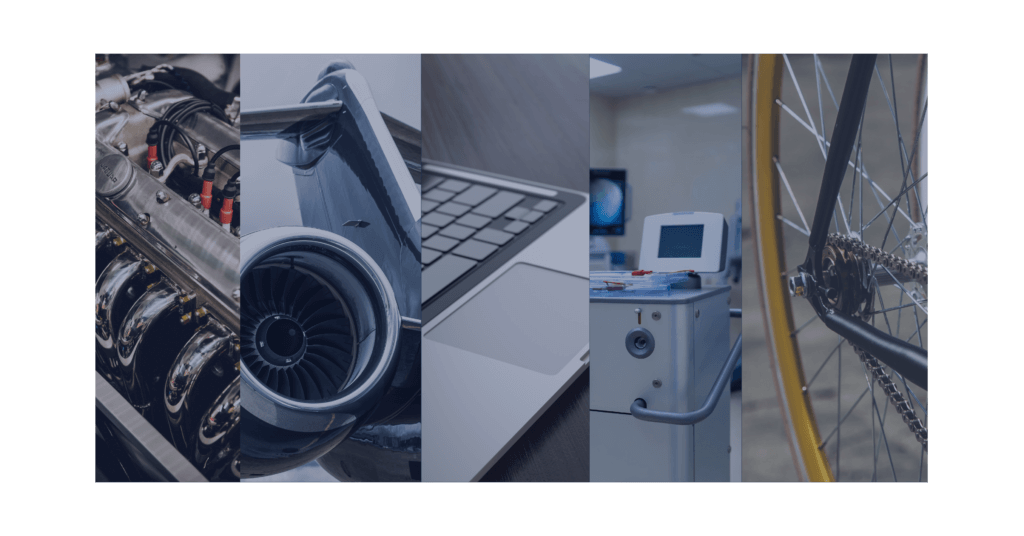
Pros & Cons of Die Casting
Die casting is a fast and efficient way to produce high-volume, complex metal parts with a high degree of precision. Here are some pros and cons of die casting:
Pros:
- High production rates: Die casting can produce many parts quickly, making it ideal for high-volume production.
- Precision: Die casting can produce parts with a high level of accuracy and surface finish, which is vital for critical applications.
- Versatility: Die casting can be used to produce parts in a wide range of sizes and shapes, from small and intricate to large and complex.
- Durability: Die cast parts are typically more robust and durable than parts made using other manufacturing processes, such as injection molding.
- Cost-effective: Die casting can be a cost-effective option for producing high volumes of parts, as the high production rates may offset the initial setup costs.
Cons:
- Limited to certain materials: Die casting is typically limited to metals with a low melting point, such as aluminum, zinc, and brass.
- Requires specialized equipment: Die casting requires specialized equipment, including a die casting machine and a mold, which can be expensive to purchase and maintain.
- Limited design options: The design of die cast parts is limited by the constraints of the die casting process, such as the need for draft angles and the inability to produce undercuts.
- Finishing may be required: Die cast parts may need additional finishing steps, such as deburring or polishing, to achieve the desired surface finish.
- Possible quality issues: Die casting can be prone to defects such as porosity, shrinkage, and surface imperfections, which can affect the quality and performance of the parts.







Zetwerk is a leading die casting company of high-quality customized die cast parts with production facilities in the USA. We offer just-in-time delivery and the broadest range of die cast products to suit all applications – from miniature and intricate models to heavy automotive components – backed by over many years of experience. Zetwerk uses state-of-the-art technology and expert knowledge to deliver the right solution every time, on time, whatever the size or complexity of your project. If you are looking for top-quality custom die cast parts without compromising production speed or turnaround times, Zetwerk is your first stop!






