Ten Things to Know Before You Die Cast Your Own Products
- Understand the process: Before you start casting your components, it is essential to familiarize yourself with the process. This typically involves creating a mold, melting and pouring the desired material (such as metal or plastic), and allowing it to cool and solidify. There are various methods for casting, including lost wax casting, sand casting, and investment casting, each with its own set of advantages and disadvantages.
- Choose the right material: The type of material you choose for casting will depend on the intended use of the finished product. Metal is a popular choice for casting, as it is strong and durable. However, it can be expensive and requires specialized equipment to work. Plastic is another option, as it is generally cheaper and easier to work with, but metal may be stronger and more long-lasting.
- Invest in quality equipment: To cast your products, you will need specific equipment, such as a furnace, molding materials, and casting tools. It is important to invest in high-quality equipment, as this will make the casting process more accessible and accurate. Cheap, low-quality equipment may break or malfunction, leading to wasted materials and frustrating setbacks.
- Create a detailed plan: Before you start casting, it is important to have a clear and detailed plan in place. This should include a detailed design of the finished product and a step-by-step guide for the casting process. This will help ensure that the finished product meets your expectations and that the process runs smoothly.
- Practice proper safety measures: Casting involves working with high temperatures and potentially hazardous materials. It is important to take adequate safety measures, such as wearing protective gear and following all safety instructions for your equipment.
- Prepare your workspace: Make sure that your workspace is clean, organized, and well-ventilated. A cluttered or poorly ventilated workspace can lead to accidents and make the casting process more difficult.
- Test your mold: Before starting the casting process, it is a good idea to test your mold. This will help you identify any issues or imperfections and allow you to make any necessary adjustments before you begin casting with the final materials.
- Pay attention to temperature: Temperature is a critical factor in the casting process. The material you are casting must be heated to the correct temperature in order to flow properly into the mold. If the temperature is too low, the material may not flow properly, leading to a poorly finished product. On the other side, if the temperature is maximized, the material may burn or become damaged.
- Use the right tools: Different casting projects will require different tools. Make sure to use the appropriate tools for the task at hand, as using the wrong tools can lead to accidents or poor-quality finished products.
- Be bold and ask for help: Casting your products can be challenging and complex, and asking for help or guidance is okay if needed. Resources such as online forums, instructional videos, and local casting clubs can provide valuable information and support. Overall, the key to successful casting is planning carefully, paying attention to detail, and being willing to learn and adapt. You can confidently create high-quality, custom-made products with the right knowledge and equipment.
Can Thorough Planning in Die Casting Save You Time and Money?
Thorough planning is essential in any manufacturing process, and die casting is no exception. Proper planning can help you save time and money by ensuring the process runs smoothly and efficiently. One of the most important values in planning for die casting is creating a detailed design for the finished product. This should include all necessary dimensions and specifications, as well as any necessary tolerances. Having a clear understanding of the desired result will help you choose the appropriate materials and equipment, and it will also help you identify any potential issues or challenges before they arise.
Another important aspect of planning is creating a detailed production schedule. This should include a timeline for each step in the process and any necessary lead times for ordering materials or equipment. A clear schedule can help you stay on track and avoid delays or setbacks. In addition to these considerations, thorough planning can also help you optimize the use of your equipment and resources. For example, by identifying potential bottlenecks in your supply chain or inefficiencies in the process, you can streamline the process and reduce waste.
Overall, thorough planning is essential for ensuring that your die casting process is successful and cost-effective. Planning each process step carefully can save time, reduce waste, and achieve the best results.





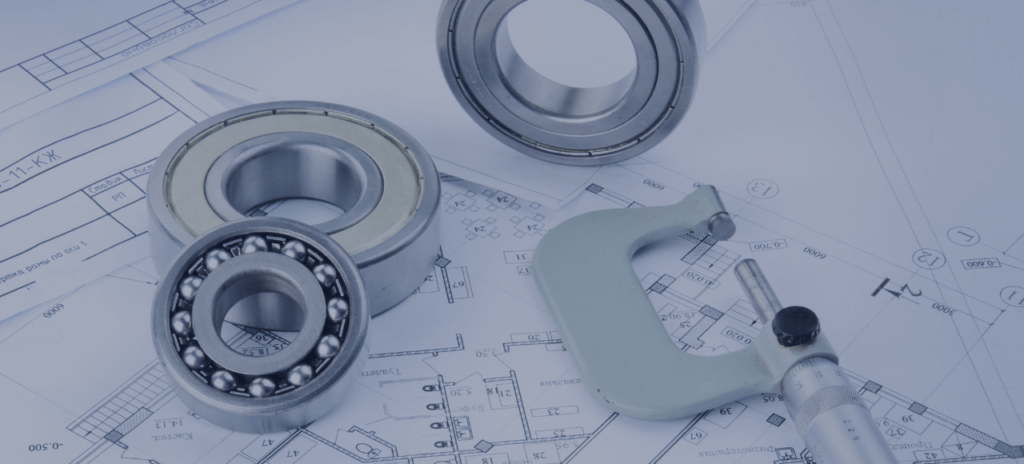
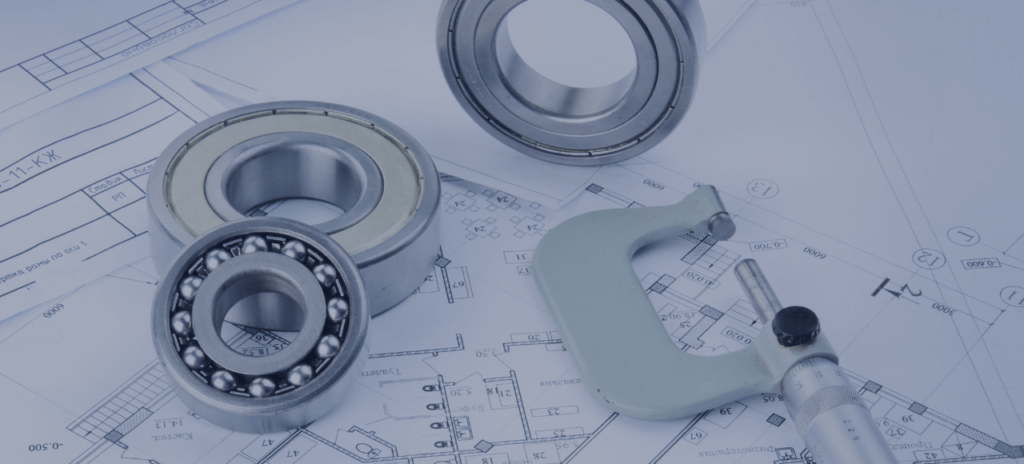
How custom die casting will help achieve your idea?
Custom die casting can help bring your idea to life by allowing you to create custom-made products with precision and accuracy. One of the major benefits of custom die casting is the ability to create highly detailed and complex parts. The mold which is used in the die casting process can be designed to produce parts with intricate shapes and features, making it a suitable choice for creating a wide range of products, including automotive components, consumer electronics, and medical devices.
Another advantage of custom die casting is the ability to produce large volumes of parts quickly and efficiently. The die casting process is highly automated, allowing for the production of thousands or even millions of parts in a short period. This makes it a cost-effective choice for producing large quantities of a single product or component. In addition to these benefits, custom die casting offers high design flexibility. The mold can be customized to meet your specific requirements, allowing you to create a product tailored to your specifications and make your idea into reality.
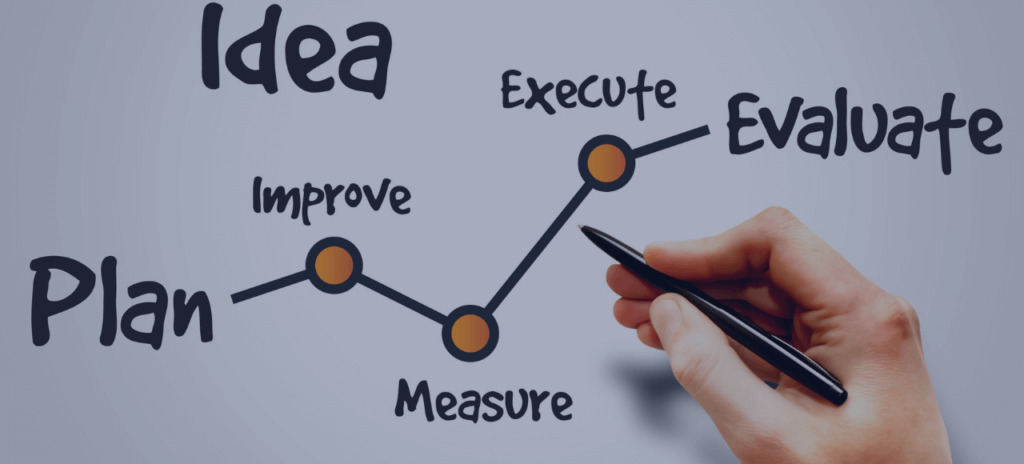
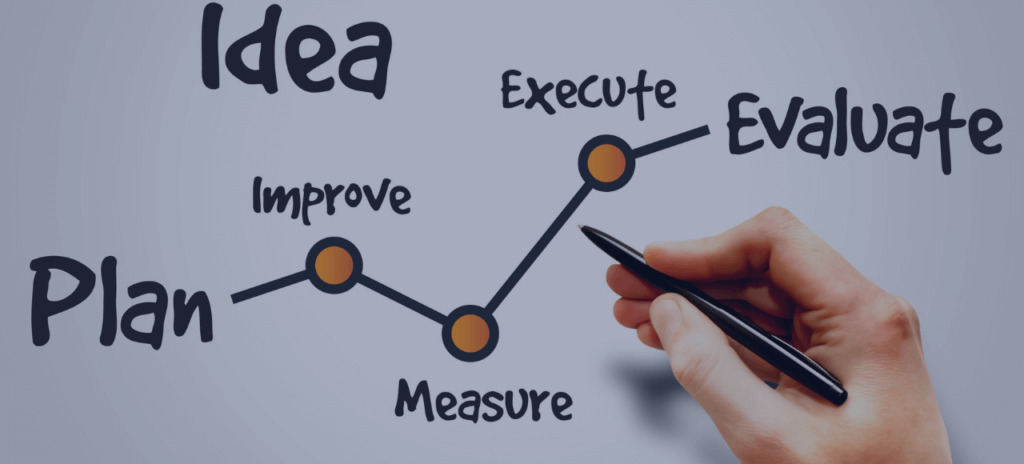