Castings made of aluminum are created by pouring molten metal into molds designed using the eventual product’s pattern as a guide. Three prevalent molding techniques used to produce aluminum are die casting, sand casting, and permanent mold casting.
The aluminum oxide layer that forms as soon as the component is removed from the mold protects against corrosion and rust, a crucial advantage of aluminum cast parts.
THE ALUMINUM CASTING PROCESS
Typically, molten aluminum is poured into a steel mold that has been precisely carved to produce a very smooth and refined surface as part of the casting process. This is one of several processes used to make aluminum castings, each of which is employed to make a certain kind of part.
Different molds, constructed of steel or a non-metallic substance, can be used to create castings. Each type is used for its dependability and product quality and has its own advantages.
Examining each of the various diverse processes and how they are applied is required in order to describe the aluminum casting process. Zetwerk gives consumers a choice of methods, in contrast to most manufacturers that concentrate on one or a few.
- Die casting: Die casting is a process for making metal objects that requires forcing molten metal into a mold under pressure. Die-cast goods are exact and require little machining or finishing. The method is quick and perfect for creating large quantities of parts. Die casting includes two types: hot and cold. While cold die casting employs a ladle to pour the molten metal into a cold chamber where it is injected with a plunger, hot die casting involves injecting molten metal into a heated chamber using a plunger.
- Permanent Mold Casting: The main cost of permanent mold casting of aluminum is the machining and shape of the mold, which is typically composed of grey iron or steel. The heated mold is cut into the two halves of the planned part’s geometric shape with specifications. Molten aluminum can be ladled, poured, or injected during the injection process. After the component has been cast, the mold must cool so the metal component can solidify. To avoid flaws in the part, it is swiftly removed from the mold after cooling. The approach is a highly advanced, scientifically created way to produce enormous volumes of parts.
- Vacuum Die Casting: A crucible of molten aluminum and a bell housing with a sprue aperture and a vacuum outlet are used in vacuum die casting. The sprue is first immersed in the molten metal to start the operation. There is a pressure difference between the molten aluminum and the die cavity in the crucible due to the receiver being made vacuum-tight. The molten aluminum flows into the die cavity because of the pressure difference, where it solidifies. The part is expelled once the die has been opened and withdrawn from the receiver. The quality of the components can be improved by regulating the part fill rate and the pressure differential and vacuum between the molten aluminum and the die cavity.The sprue will be free of oxides and dross if buried beneath the aluminum’s molten surface. There are few foreign elements, and the parts are sound and clean.





- Lost Foam Casting: Polystyrene foam is substituted for wax in the lost foam casting procedure, a form of investment casting, to create the pattern. Mold cavities filled with polystyrene beads are filled with low-pressure steam that is injected into aluminum molds to produce the pattern. The design is positioned in dry, vibration-compacted sand to stop air bubbles from developing in the casting. The foam is burned off, and casting is created by pouring molten aluminum into the sand mold.
- Sand Casting: Sand casting entails packing sand around a reusable mold that replicates the shape, features, and configuration of the finished product. A riser makes it possible to pour molten metal into the mold, preventing porosity due to shrinkage. A sprue that enables the insertion of molten metal into the mold is part of the design. Shrinkage that occurs while cooling is accounted for by the sprue, which has a diameter slightly bigger than the finished product. Because each mold must be filled with molten metal, the sand maintains its shape while bearing the weight of the metal and is impervious to contact it.
- Investment Casting: Wax patterns are injected into the die to form the finished product in the investment casting process. The wax is fastened to a sprue, creating a structure resembling a tree. A ceramic shell is made around the wax shape by repeatedly dipping the tree into a slurry. After the ceramic has dried and solidified, the wax is burned off in an autoclave. Before being filled with molten aluminum, which is poured into the sprue and then travels via a series of runners and gates into the molds, the shell is heated to the correct temperature. These components are made of wood that has been cut into the shape of trees, and after they harden, the ceramic shells are knocked off.
ALUMINUM ALLOYS IN ALUMINUM CASTING PRODUCTS
The first three numbers in a system used to identify aluminum alloys identify the alloy with which aluminum has been mixed. These numbers are followed by a decimal point, a number identifying the product’s shape, such as casting or sheet metal, and finally, another number. A crack, corrosion, finishing, and joining number is also assigned to each alloy, ranging from one to five, with one denoting the best and five the worst. All categories for the alloys in the 1000 series are rated as one, while all 8000 series are rated as five.
- 1000 Series: The alloy with the highest purity, the 1000 series, has 99% aluminum. It is quite workable and soft, and ductile. Due to its slow hardening, the 1000 series can withstand intense shaping. It works well during processing and is simple to weld.
- 3000 Series: Manganese serves as the series 3000’s main alloying component. Although it is only moderately strong, the manganese and aluminum combination provides considerable corrosion resistance. It is a heat-treated, non-reinforced alloy of aluminum. The series 3000’s low density, high plasticity and weldability, resistance to corrosion, ductility, and very smooth final surface are its key advantages.
- 5000 Series: The 5000 series has a magnesium alloy, which significantly improves its tensile strength and formability. It is categorized as high weldability, high strength sheet, and plate alloy. Because of its resistance to acid and alkali corrosion, the 5000 series is preferred for sheet metal applications. The 5000 series can adapt to severe, hostile settings thanks to these qualities.
- 7000 Series: The aluminum alloys in the 7000 series are the toughest and most durable, with a strength factor that is equivalent to that of industrial-grade A3 steel. The 7000 series’ remarkable wear resistance, good mechanical qualities, and anode reaction are all a result of its high hardness. It is perfect for casting objects like airplane parts that must withstand a lot of tension. Although zinc has the same hardness as aluminum on the Mohs scale, it is an alloy of 7000 aluminum that helps to boost its hardness.
- 2000 Series: The 2000 series are alloyed with copper, which ranges in content from 2% to 10%, as well as trace amounts of other elements. Aluminum’s strength and hardness are increased by the copper, but its flexibility and resistance to corrosion are decreased. Although difficult to weld, Series 2000 can be heat treated.
- 4000 Series: The addition of silicon to the 4000 series alloy lowers the alloy’s melting point and increases its fluidity. Due to how simple it is to form it when it is molten, it is one of the more widely used casting alloys. As a filler for brazing and welding, the 4000 series is employed.
- 6000 Series: Magnesium and silicon are added to the 6000 series alloy to offer it strength, mechanical characteristics, and corrosion resistance. To improve the 6000 series quality, several variants have been blended with series 4000 and 5000. The 6000 series processing involves complex, high-tech equipment that is specialized and expensive. The simplicity with which it can be coated and treated, as well as its workability, go hand in hand with its outstanding resistance to corrosion and oxidation.
- 8000 Series: Tin is the main component of the 8000 series’ principal alloy, with trace amounts of copper and nickel. Despite having a low strength, this alloy possesses excellent machinability and wear resistance. The 8000 series alloy composition varies depending on the intended purpose of the finished product. The metal’s density, stiffness, and temperature performance are all governed by its arrangement.
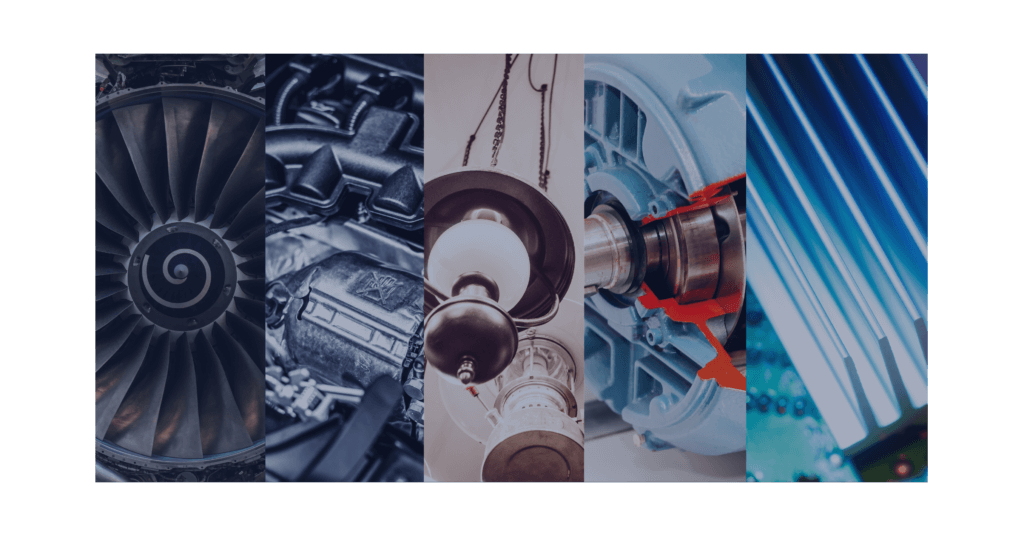
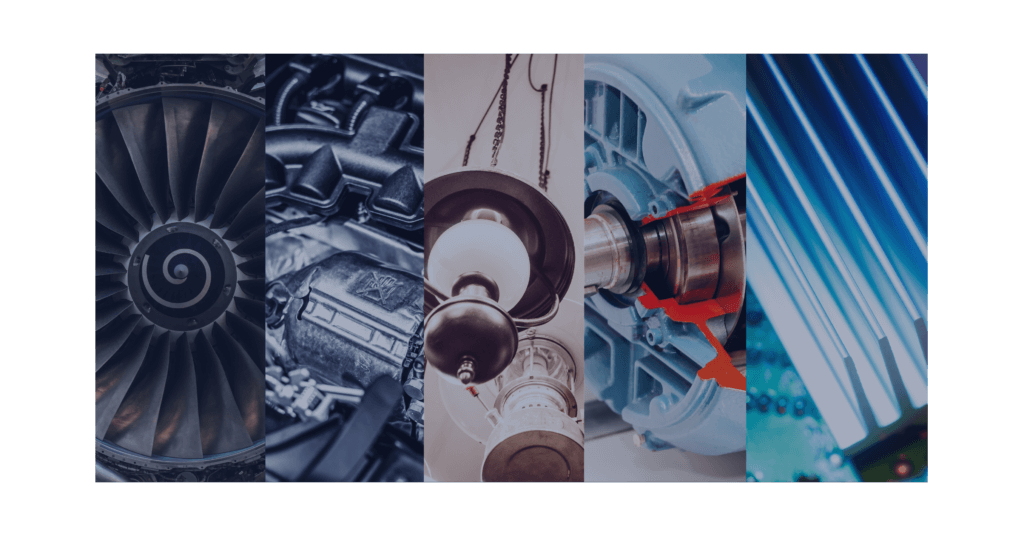
Industrial Aluminum Casting Products
Aluminum has become a key component in the production and creation of a wide range of commercial and industrial aluminum goods ever since the Bayer and Hall-Héroult techniques for processing and refining aluminum were developed. The emergence of more efficient and practical production techniques allowed engineers and designers to include aluminum in their renderings quickly.
Aluminum’s various qualities and traits have shown it to be a dependable and durable metal with a long service life as well as the capacity to be machined and molded into any shape to meet a design, from ovens to airplanes. More than 270 minerals can be mixed with aluminum to improve its properties.
- Aircraft Components: Since World War II ended, the aerospace sector has relied on aluminum parts, which make up about 80% of an aircraft’s structure. Cast aluminum parts have the qualities and traits that the industry requires. Cast aluminum components have allowed aircraft manufacturers to save a significant amount of money.
- Agricultural Equipment: Similar criteria and specifications apply to many of the aluminum cast parts used in agriculture as they do in the auto sector. Due to the severe environments and regular use, agricultural machinery needs greater strength and long-lasting stability. Cost is another element that is very important for agricultural output. Crankcase housings, gearbox housings, and motor housings all require aluminum castings because of these factors.
- Heatsinks: A heatsink’s purpose is to take heat away from parts and components made for electronic purposes. Cast aluminum heat sinks require less machining, which reduces production costs and speeds up production. The additional heat sink features, including cooling fins, are created concurrently, significantly increasing production efficiency. Cast aluminum heat sinks can be grounded because they are electrically conductive. To avoid auxiliary activities like machining and assembly and cut costs, they are cast with additional characteristics.
- Brackets: Manufacturing brackets for industrial and domestic appliances, as well as heavy-duty equipment, is a typical use for the aluminum casting process. Due to the finished bracket’s almost net shape and the use of aluminum casting, no welding or assembly is required. Aluminum brackets are made from a single piece, making them stronger and less likely to break. When holes are required, they are added to the casting mold so that finishing is not required.
- Enclosures: Sensitive electronics can be housed in aluminum cast enclosures in any kind of setting. Aluminum’s inherent level of shielding against radio frequency interference (RFI) and electromagnetic interference makes it a good choice for enclosures (EMI). Aluminum casting’s seamless design produces a sealed, watertight container that can endure any kind of circumstance.
- Golf Product: Manufacturers now use aluminum casting to create golf equipment because of its strength, stability, and capacity for producing a variety of shapes. Producers want to help gamers get better gear at a reduced price so they can play better. Golf ball warmers, clubs, handles, and brackets are a few examples of the various golf product categories.
- Military: Aluminum casting is used to make a variety of parts and components for the military that must adhere to strict government regulations. The qualities and features of the materials, as well as the fabrication and processing of military parts, are described in detail. Military parts are highly specialized, which presents a challenge to manufacturers because every military part requires precise engineering and meticulous attention to detail.
- Lighting: Lightweight, non-toxic lights are produced via aluminum cast lighting. Light fixtures made of aluminum cast are perfect for outdoor use since they are resistant to corrosion. The permanent mold and gravity casting techniques, which make it simpler to deal with the finished product and may be utilized for lighter forms of aluminum, are two widely used methods for creating lighting fixtures. Cast aluminum is a cost-effective and time-saving material for making light fixtures, much like it is for making automobile parts. Any design can be produced using any of the several production methods with ease and will have the necessary stability and features. Aluminum cast lighting’s appeal is mostly due to its simplicity of manufacture, lightweight, and outstanding robustness.
- Automotive: Automobile manufacturers are constantly looking for ways to use high-strength aluminum castings in their product designs as the demand to increase gas efficiency for vehicles has increased. Aluminum casting manufacturers have been refining and enhancing their procedures and techniques to speed up production and improve output at a fair price to help with the process. Oil Pumps, Water Pump housings, Connector, Transmission parts, and a wide variety of brackets are just a few of the aluminum C Aluminum cast components that have become crucial components in advancements and developments in automotive design due to their strength and dependability.
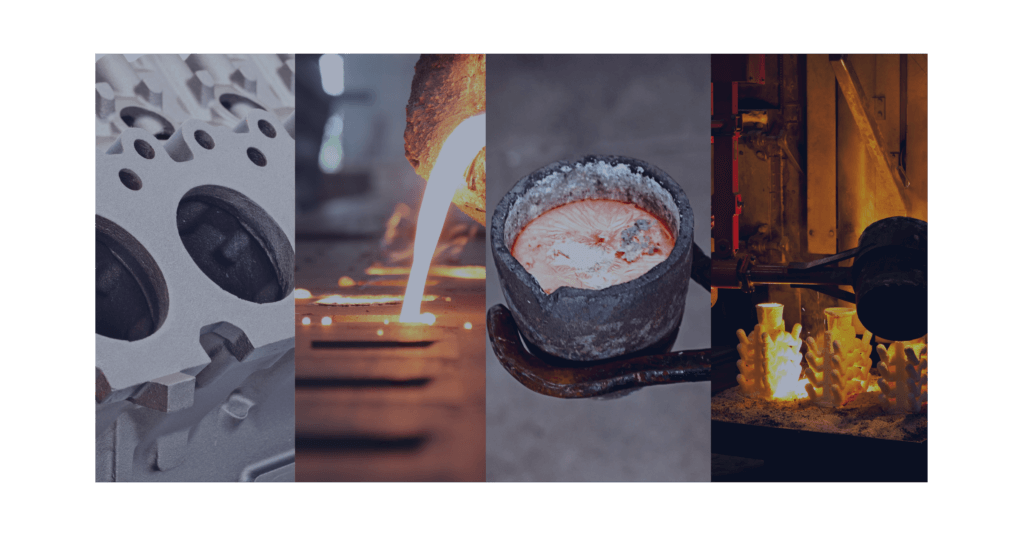
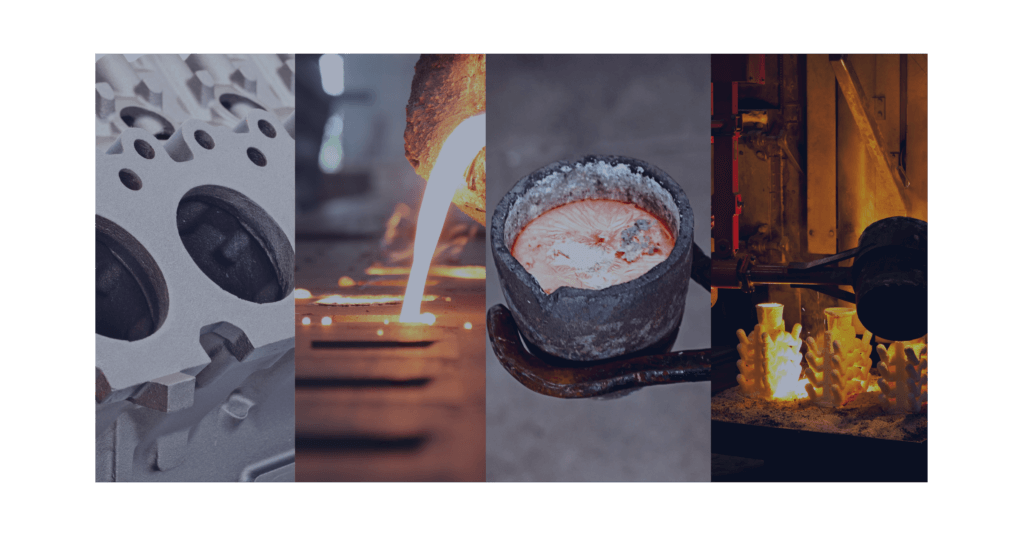
By pouring molten aluminum into a properly manufactured and precisely designed die, mold, or form, aluminum casting is a technique for making high tolerance and high-quality parts. The layer of aluminum oxide that forms as soon as the item is taken out of the mold is a benefit of aluminum cast parts. The layer of aluminum oxide is a layer against rust and corrosion. Pouring molten aluminum into a steel mold that has been precisely machined to produce a cast object with an incredibly smooth and refined surface is a standard way to cast aluminum. Since there is more than one step involved, it is important to look at each one in order to understand how the aluminum casting process works. With oxygen and silicon coming in first and second place, respectively, and aluminum being the most common metal, aluminum is the third most common element on earth.




