The process begins by creating a die or mold from a hardened tool steel. The die is typically machined to the desired shape of the final part and includes a sprue, runner system, and one or more cavities. The die is mounted onto a die casting machine and heated to the appropriate temperature for the specific aluminum alloy being used.
Next, the molten aluminum is heated to a temperature above its melting point and injected into the die under high pressure using a hydraulic plunger or a screw-type injector. The high pressure forces the aluminum to fill all the voids in the die, including the intricate details and tight tolerances. Once the aluminum has solidified, the die is opened, and the casting is ejected. Several different types of aluminum alloys can be used in the die casting process, each with unique properties and characteristics. Some common alloys include A380, A383, A360, and 214. The choice of alloy will depend on the specific requirements of the part being produced, such as the required strength, corrosion resistance, and thermal conductivity.
After the casting has been ejected from the die, it will typically undergo a series of post-processing operations to achieve the desired finish and meet any functional requirements. These operations may include machining, deburring, polishing, and surface treatment. One of the benefits of aluminum die casting is the ability to produce parts with complex geometries and intricate details that would be difficult or impossible to achieve using other manufacturing processes. The process is also relatively fast and can have high volume runs at a low cost. However, the tooling costs can be high, and the process could be better suited for producing small runs or parts with thin walls.
Aluminum Casting Cost & Product Lifetime
The cost of aluminum casting depends on multiple factors, including the complexity and size of the part being produced, the type of aluminum alloy used, and the number of parts produced. Costs associated with aluminum casting can also be impacted by
- die casting process
- finishing and tolerances
- post-processing operations that may be required.
In general, aluminum casting can be a cost-effective manufacturing option for producing high volume runs of parts with complex geometries and tight tolerances. The initial tooling costs may be higher compared to other manufacturing processes. However, the cost per part is typically lower due to the ability to produce a large number of components in a single run.
The life cycle of an aluminum casting depends on the specific application and environment in which it is used. Some aluminum alloys are more resistant to corrosion and wear than others, which can affect the overall life cycle of the casting. Proper design, material selection, and maintenance can also help extend the life of aluminum casting components.





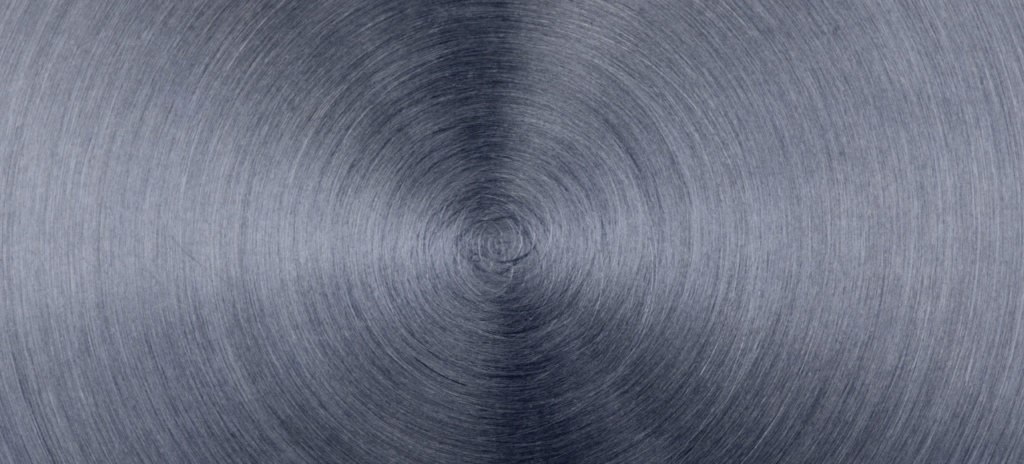
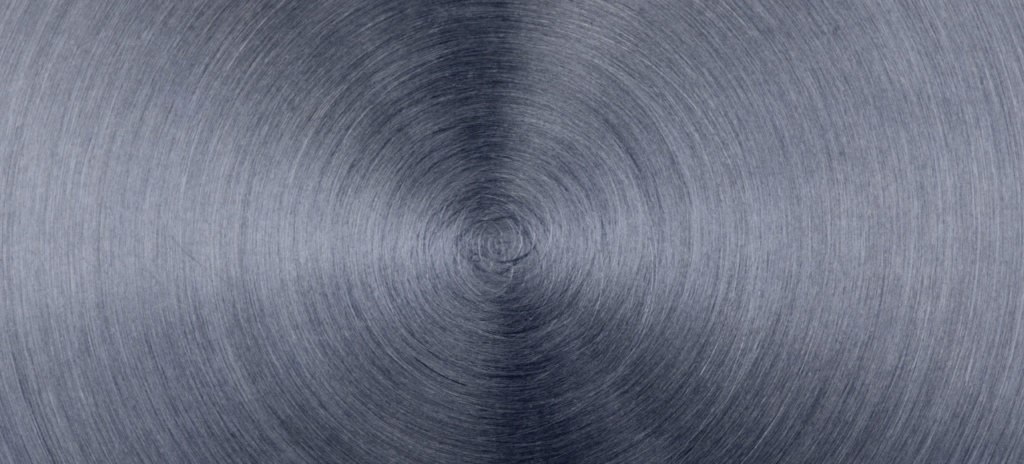
How Much Does Aluminum Die Casting Cost?
Tooling, casting, and finishing are the three major elements of the total price of aluminum die casting. The cost of producing the mold used to mass-produce the components is known as “tooling.” This is an initial expense that is spread out during the die. However, it can vary depending on the complexity of the part.
The term “casting costs” refers to the total amount spent on making the parts through the casting process, including the aluminum’s price, the cost of operating the machinery, and any additional expenses incurred. Depending on the market, the price of aluminum might range anywhere from $1 to $3 per pound. Depending on the scale of the project requirement and the aluminum casting companies productivity, the cost of running the machinery and other expenses related with the casting process might range widely.
Any extra labor required to modify the cast components is considered a finishing charge. Machine work, polishing, painting, and assembly are all examples of this. Pricing for finishing might range widely based on factors, including the part’s complexity and the desired detail level.
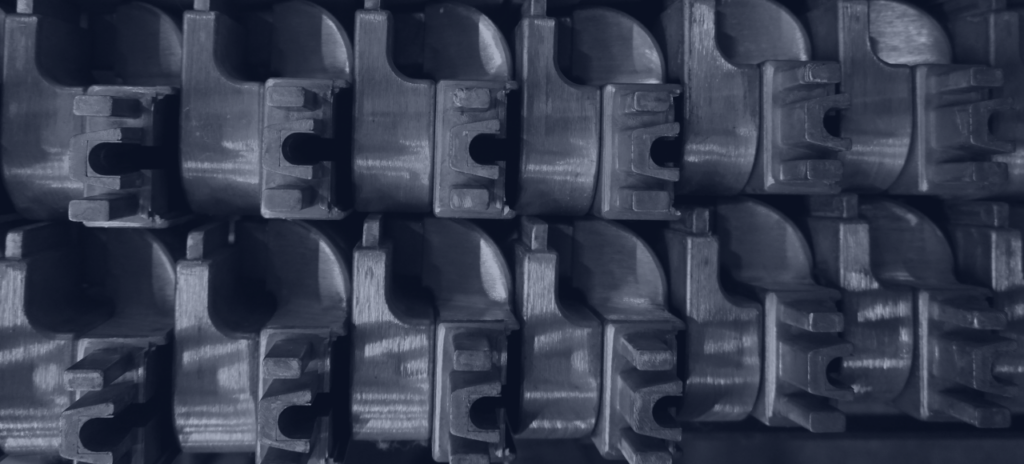
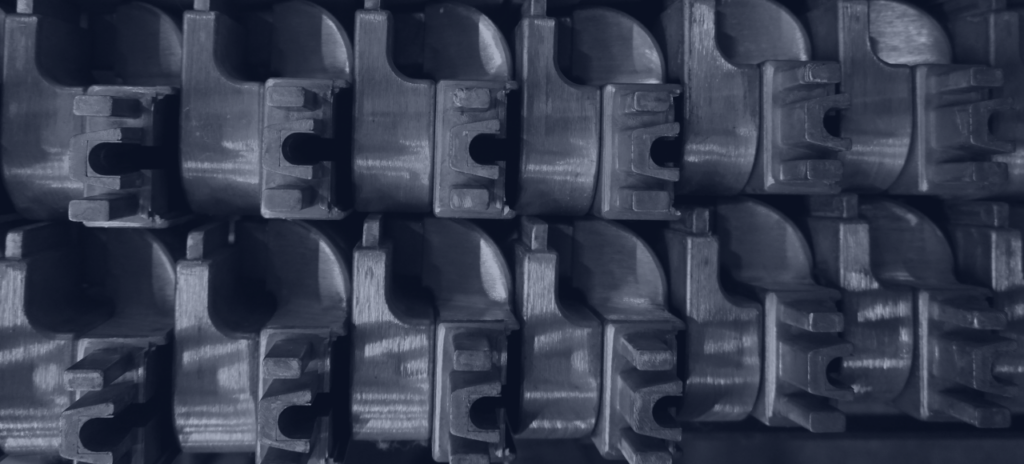
According to the variables mentioned above, the price of a single aluminum die cast component can change from a few cents to several dollars per component. Contacting a die casting company for an in-depth quotation is recommended. They can give you an estimate that considers everything from the price of tools and molds to the cost of castings and the labor required to apply finishes.




