Aluminum Casting Overview
The aluminum casting process is a tried and accurate manufacturing process that allows for the highest quality in the industry. In this process, molten aluminum is poured into a mold and allowed to solidify, forming solid aluminum parts or products. The process involves heating aluminum to a liquid state, then pouring it into a mold where it cools and solidifies into the desired shape. The process allows the creation of precision components with intricate shapes and design details.
There are several different molding techniques for aluminum casting, including:
- Sand casting
- Permanent mold casting
- Die casting
Sand casting is a common method in which a mold is created by packing a mixture of sand and binder around a pattern. The pattern is then removed, leaving a cavity in the shape of the desired part. Molten aluminum is poured into the cavity and allowed to solidify.
Permanent mold casting involves using a reusable metal mold, typically made of steel or cast iron. The molten aluminum is poured into the mold and allowed to solidify. The finished part is then removed from the mold.
Die casting is a process in which a metal die is used to shape the molten aluminum as it is injected into the mold under high pressure. This method often produces parts with complex shapes or fine details.
Overall, aluminum casting is a versatile and cost-effective way to produce a wide range of parts and products. Aluminum is used in various industries, including Defence, Medical, automotive, aerospace, Electronics, and General Engineering.
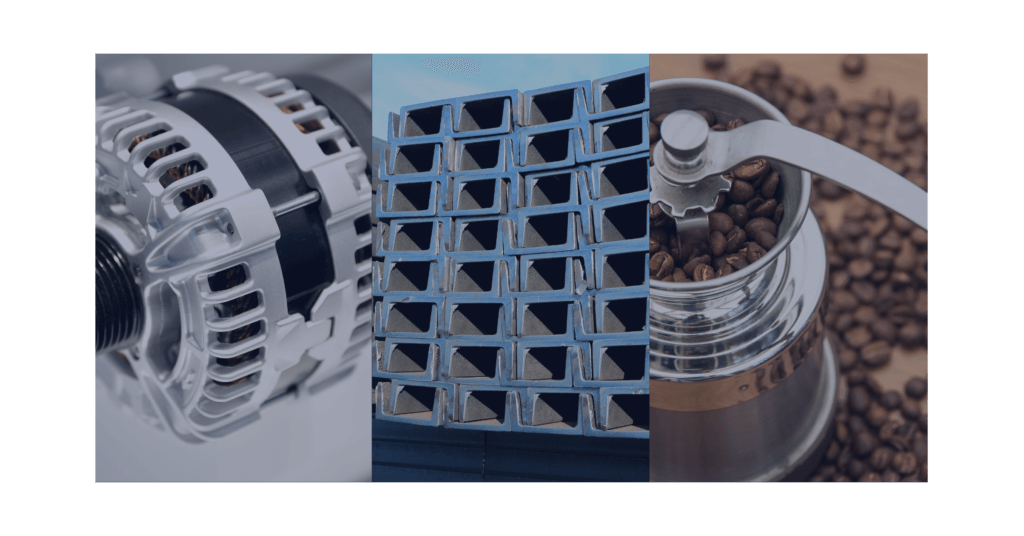
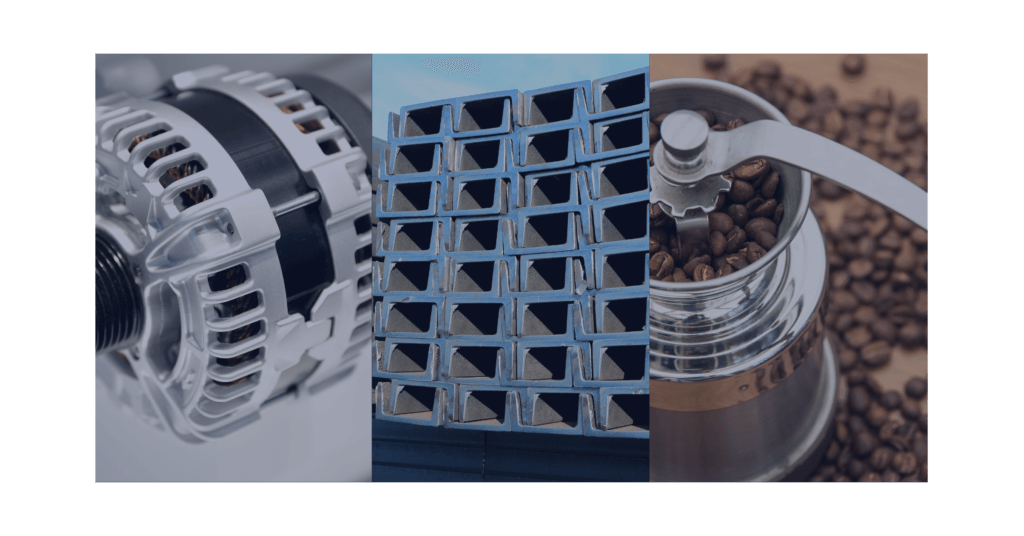
Benefits Of Aluminum Casting
There are several benefits to using aluminum casting parts in manufacturing:
- Design flexibility
Aluminum casting allows for a wide range of design options, including complex shapes and intricate details, making it suitable for use in various applications.
- Cost-effective
Aluminum casting is often more cost-effective than other casting methods, particularly for high-volume production runs.
- Versatility
Aluminum can be cast into a wide range of shapes and sizes, making it suitable for various applications.
- Ease of machining
Aluminum is relatively easy to machine, making it suitable for applications requiring precise tolerances and smooth finishes.
- Ease of machining
Aluminum is relatively easy to machine, making it suitable for applications requiring precise tolerances and smooth finishes.
- Precision
Aluminum casting can produce parts with high levels of precision and accuracy, making it suitable for use in applications where tight tolerances are required.
- Lightweight
Aluminum is much lighter than other metals, making it ideal for applications where weight is a concern, such as in the automotive and aerospace industries.
- Strong and durable
Despite its lightweight, aluminum is a solid and durable metal that can withstand high levels of stress and strain.
- Corrosion resistance
Aluminum has excellent corrosion resistance, making it suitable for outdoor and marine environments.
- Good thermal conductivity
Aluminum has good thermal conductivity, making it an excellent choice for heat exchangers and other applications where heat transfer is essential.
- High recyclability
Aluminum has a high recycling rate and can be recycled indefinitely without losing quality, making it an environmentally friendly choice for many applications.
Applications of Aluminum Casting
Cast aluminum is a widely used method for producing parts and components for a variety of applications, including:
- Automotive: Aluminum castings are commonly used in automotive components such as engine blocks, transmission cases, and cylinder heads.
- Aerospace: Aluminum castings are used in the aerospace industry for structural components, engine parts, and other applications where lightweight and high-strength materials are required.
- Construction: Aluminum castings are used in the construction industry for products such as window frames, doors, and roofing materials.
- Marine: Aluminum castings are used in the marine industry for boat hulls, propellers, and other parts that must resist corrosion.
- Military: Aluminum castings are used for various applications, including weapons, armor, and other equipment.
- Medical: Cast aluminum is used in the medical industry for products such as prosthetics, surgical instruments, and other medical devices.
- Consumer products: Casting aluminum is used to produce a wide range of consumer products, including appliances, cookware, and other household items.





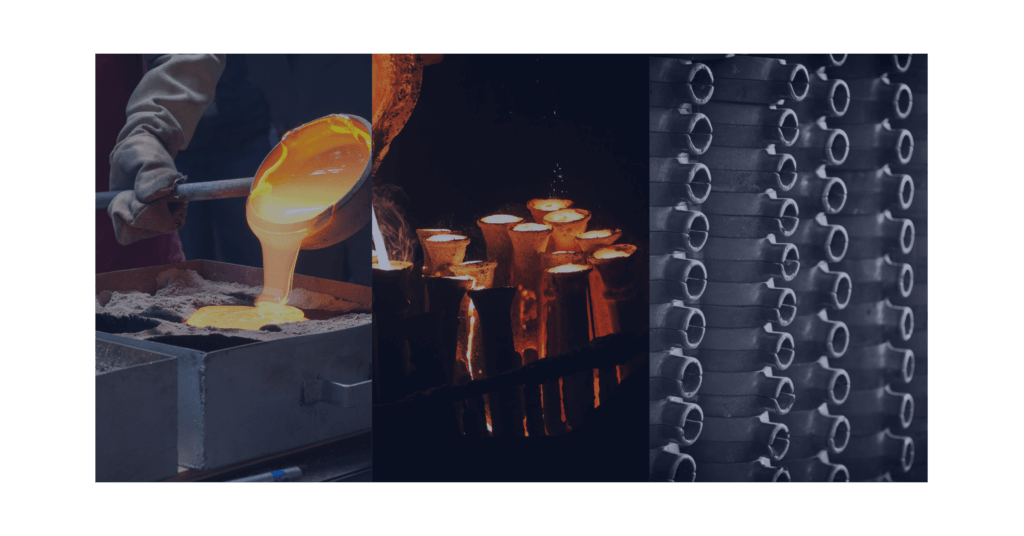
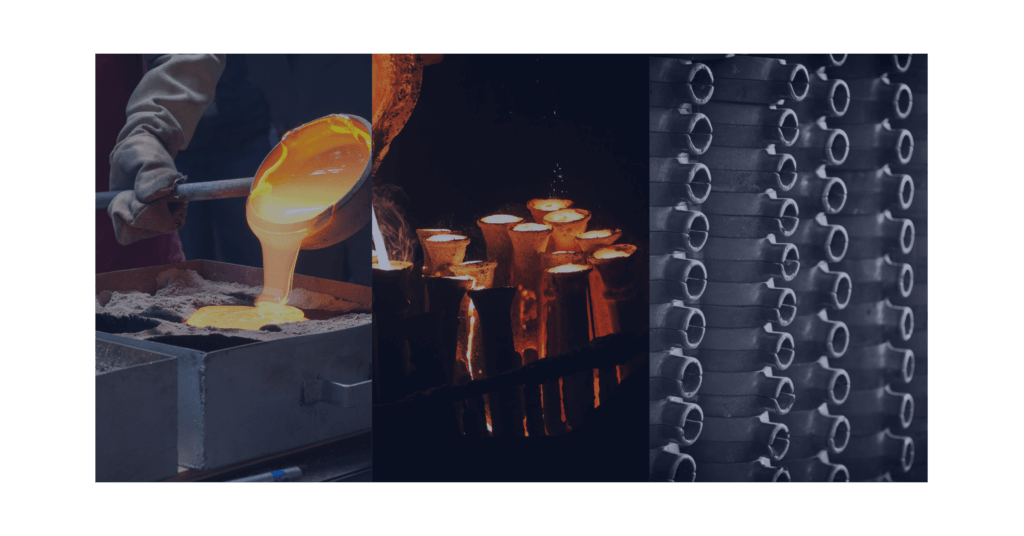
Zetwerk is an aluminum casting company and one of the leading companies in processing, fabricating and supplying quality aluminum value-added products. We have been in business for many years and work with various clients to create innovative solutions for their businesses. We have experience in the casting business and the knowledge to ensure your business is booming. Our clients rely on us for premium-quality products that are reliable, durable, and versatile.




