A manufacturing process that creates high-quality products by using computer-controlled, automated machines; precision machining is used in many industries, including aviation, automotive, and construction, to name a few. Read on to learn more about this process and how it can be used to your advantage in the workplace or at your business!
Precision machining is a manufacturing process involving computer-controlled tools to produce high-tolerance, multifaceted parts. It’s often used to manufacture parts that are difficult to produce by other methods. Precision machining can be further broken into two subcategories: surface grinding and precision turning. Surface grinding includes processes like lapping (which uses abrasives) and honing (which uses abrasives on a machine). This process creates flat surfaces on irregularly shaped components or removes burrs from edges after cutting sheet metal with shears or lasers.
The end result is usually a mirror-like finish with tolerances less than 0.001 inches per side seam length; however, these tolerances vary depending on how much material must be removed from an area before it meets dimensional specifications for final assembly into your finished product. Precision turning refers to machining cylindrical components from bar stock using high-speed lathes explicitly designed for this purpose – rather than milling them out using conventional machines equipped with circular saw blades attached directly to their spindles.
The most common types of machining processes used in the manufacturing industry include:
– Lathe turning: A lathe is a machine that uses rotating cutting tools to shape metal stock into parts with high precision. Lathe turning is typically used on large materials such as blanks for engine blocks or aircraft landing gear leg castings.
– Milling: Milling involves using a tool called an end mill to cut away material from a piece of metal until it reaches its final form. It’s often used when making parts out of sheet metal because it leaves smooth edges without creating chatter marks or other defects in the finished product.
– Grinding: Grinding involves using abrasive wheels or belts to remove material from an object until its desired shape has been reached. Grinding is often used when working with softer materials.
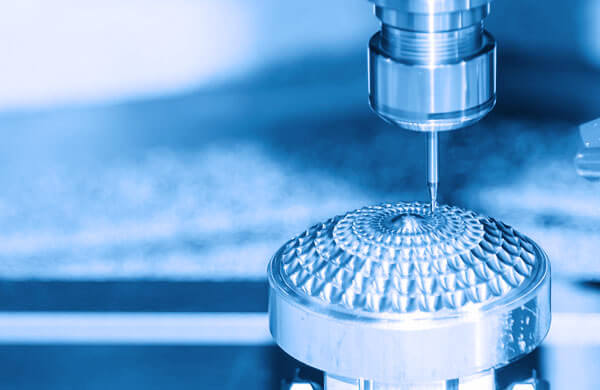
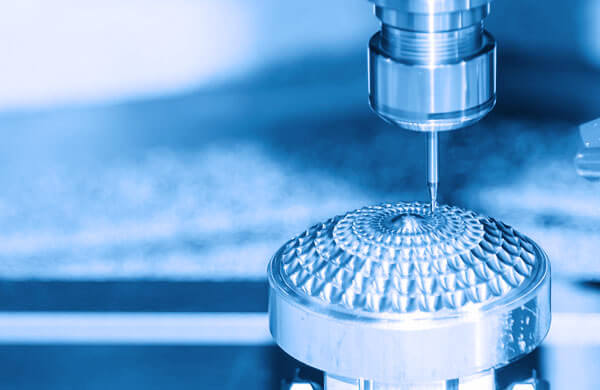
TYPES OF PRECISION MACHINING
CNC MACHINING
CNC machining is cutting material using a computer, numerically controlled (CNC) machine tool. This process is used to make parts that are too complex or too large for humans to produce by hand. CNC stands for Computer Numerical Control and is a method of controlling a machine tool with a digital controller. The controller creates instructions from a set of programmable parameters and transmits them to the machine’s drive system to produce desired motion in the workpiece.
The most common application for CNC machining is in the aerospace, automotive, medical, and consumer electronics industries. These industries use CNC machines for creating custom parts that cannot be created by other means, such as stamping or casting.
Other industries such as defense manufacturing, energy production, and construction use CNC machines to fabricate prototype parts before production runs on traditional manufacturing equipment. One of the biggest advantages of using CNC machines is that they allow manufacturers to cut costs while increasing quality and productivity simultaneously.
IN-MOLD MACHINING
In-mold machining is a manufacturing process that combines injection molding and machining. The process allows for the creation of complex parts with minimal post-processing. In-mold machining has many uses but is most commonly used in the automotive industry. In-mold machining involves two main steps: molding and machining. First, a metal or plastic mold is created using traditional injection molding techniques. Then, the part is removed from the mold and machined using CNC milling or lathe tools. This process can be repeated multiple times until the desired shape is achieved.
Benefits of In-mold Machining
There are many benefits associated with in-mold machining including:
Reduced manufacturing time:
Traditional manufacturing methods require removing parts from molds after each pass through the machine tool, which can take time and cause quality issues due to material warping or distortion during cooling periods between passes. With in-mold machining, only one pass through the machine tool is needed because there are no cooling periods between each pass through the machine tool since all raw material removal occurs within the same tooling cavity as part removal occurs.
MULTI-AXIS MACHINING
The use of multi-axis machining (MAM) has increased recently as the technology has become more affordable. MAM is a form of CNC programming that allows the machine to move simultaneously in different directions rather than just one at a time. The first MAM machines were used on single-axis machines, but today they can be found on both vertical and horizontal milling machines. The benefits of using MAM include:
Improved accuracy – MAM machines are less likely to make mistakes when cutting due to their ability to move in multiple directions simultaneously, reducing human error when programming or operating them.
Reduced cycle times – By moving faster, multi-axis machining allows for faster production times. This is especially true if you work with large parts or parts requiring multiple passes through your machine daily.
Increased flexibility – You no longer have to worry about keeping your tool on center since your machine will automatically compensate for slight misalignment caused by tool wear or operator error during setup or operation.
MICRO-MACHINING
Micro-machining is a technology that allows engineers to manufacture parts with dimensions as small as one micrometer, which is equal to one millionth of a meter. Micro-machining involves electromechanical processes such as milling, drilling, grinding, and turning to fabricate tiny components. It is also used to create microfluidic devices and integrated circuits (ICs) in order to produce miniature electronic devices such as computer chips or integrated circuits (ICs).
The main advantage of using micro-machining technologies over conventional manufacturing methods is that it can significantly reduce the cost of production and help manufacturers cut down on their production cycle time. In addition, it can improve product quality by increasing the accuracy and reliability of products.
The significant micro-machining applications include:
- Analog ICs and digital ICS
- Microfluidics
- Micromechanical systems (MEMS)






INJECTION MOLDING
Injection molding is a process that uses high temperature and pressure to compress powdered plastic, metal, or other materials into the desired shape. It is used in the manufacturing of everything from toys to car parts. Injection molding is one of the most important processes in modern manufacturing. It allows for the creation of many different shapes and sizes of objects at once, which speeds up production time and lowers costs.
Injection molding has been around since the late 19th century when it was first used to create mass-produced items like toothbrushes and shoe horns. Since then, it has spread into nearly every industry imaginable, allowing manufacturers to produce everything from nails to cars in large quantities quickly and efficiently.
Injection Molding Process
The injection molding process is relatively simple: First, a mold is created with two halves (or more) that fit together snugly when closed; this forms a cavity into which molten plastic or metal can be injected. Then, after being heated until liquid, the material is forced into this cavity through an opening called a gate — much like injecting toothpaste into its tube — where it’s allowed to cool before being ejected from the die.
Process Controls
Process controls are used to ensure repeatability and quality, as well as safety, cost-effectiveness, environmental awareness, and compliance.
PRECISION MACHINING IN ACTION
The machining process begins with a model of the desired part being created in CAD software on a computer. The model is then converted into a G-code file which controls the machine tool’s movements during production. This allows for precise machining operations to be done quickly and efficiently, resulting in high-quality parts at a low cost that is accurate down to fractions of an inch!
PRECISION MACHINING INDUSTRY
The precision machining industry is highly technical and specialized. It’s important to know the basics of how it works, who does it, and what challenges they face. The precision machining industry is constantly changing as technology advances. In fact, new advancements in precision machining are opening up opportunities for people with unique skills to find work in this industry.
Companies are looking for individuals who can help them meet demand by developing new products or improving existing ones using modern manufacturing techniques such as additive manufacturing (3D printing). The future looks bright for those interested in pursuing careers in this field because many job openings will likely become available over time due to retirements from older generations retiring from their positions.