In the vast space of component manufacturing, a specialized process stands out for its precision and versatility: turned parts manufacturing. This technique, often associated with brass turned parts and other metals, is a cornerstone in various industries, from automotive to aerospace. As we delve into the intricacies of this manufacturing method, we’ll explore its significance, applications, and the value it brings to businesses.
The Basics of Turned Parts Manufacturing
Turned parts manufacturing refers to producing intricate components by rotating a workpiece and using a cutting tool to shape it. This method predominantly uses lathes, a machine that holds and spins the material while the tool cuts, shapes, or forms the piece. Brass turned parts are particularly popular due to brass’s malleability and excellent conductivity. However, various metals and materials can undergo this process, each offering unique properties suitable for specific applications.
Why Turned Parts Manufacturing is Crucial
- Precision and Accuracy: One of the primary benefits of using a turned parts manufacturer is their unparalleled precision. The lathe ensures that the component is symmetrical and meets the required specifications.
- Versatility: Whether it’s brass turned parts or components made of steel, aluminum, or plastic, turned parts manufacturing caters to a wide range of materials.
- Efficiency: Given the automated nature of modern lathes, manufacturers can produce large quantities of components quickly, ensuring timely delivery for large-scale projects.
Applications Across Industries
Turned parts manufacturing isn’t limited to a single sector. Its versatility ensures its presence in multiple industries:
- Automotive: Precision is paramount in the automotive industry. From engine components to intricate dashboard parts, turned manufacturing plays a pivotal role.
- Aerospace: The aerospace sector demands components that are both lightweight and durable. Turned parts, especially brass and aluminum ones, fit the bill perfectly.
- Construction: In construction, the strength and durability of materials are crucial. Turned parts manufacturing ensures that bolts, screws, and other fixtures are up to the mark.
- Manufacturing: Be it machinery, tools, or equipment, turned parts are integral to the manufacturing sector, ensuring that devices function optimally.
Advanced Techniques in Turned Parts Manufacturing
As technology advances, so does the component manufacturing. While still prevalent, traditional methods are now complemented by state-of-the-art techniques that enhance precision and efficiency.
CNC Turning
Computer Numerical Control (CNC) turning has revolutionized turned parts manufacturing. This method employs computerized controls to operate and manipulate the lathe, ensuring even higher accuracy in component production. The ability to program the machine allows for creating intricate designs that were once deemed challenging or impossible with manual methods.
Multi-Axis Turning
While traditional lathes operate on two axes, X and Z, modern lathes can function on multiple axes. This multi-axis turning capability allows the machine to perform drilling or milling operations simultaneously with turning. Such a feature reduces the need for secondary operations, ensuring faster production times and enhanced precision.
Challenges in Turned Parts Manufacturing
Like any other manufacturing process, turned parts manufacturing faces its set of challenges:
- Material Limitations: While materials like brass, aluminum, and steel are commonly used, some materials resist the turning process due to their hardness or brittleness.
- Tool Wear: Continuous machining can lead to tool wear, affecting the quality of the turned parts. Regular maintenance and tool replacement are essential to maintain the desired precision.
- Complex Designs: While advanced techniques have made it easier to produce intricate designs, some designs still need to be revised due to their complexity or ultra-fine detailing.
Future of Turned Parts Manufacturing
The future looks promising for turned parts manufacturing. With continuous technological advancements, the boundaries of what’s possible keep expanding. Automation, coupled with artificial intelligence, might soon play a pivotal role in further enhancing the precision and efficiency of the process. Moreover, as industries demand more customized solutions, turned parts manufacturers will need to adapt, innovate, and offer bespoke solutions to meet these evolving needs.
Innovations in Materials and Techniques
As we look beyond the current landscape of component manufacturing, it’s evident that innovations in materials and techniques will play a pivotal role in shaping the future of turned parts manufacturing.
Advanced Materials
Introducing new, advanced materials promises to redefine the capabilities of turned parts manufacturing. These materials, designed to be more durable, lightweight, and adaptable, can cater to specific industry needs. For instance, the development of high-strength, corrosion-resistant alloys can enhance the lifespan and performance of components in challenging environments.
Hybrid Manufacturing
Hybrid manufacturing combines the strengths of additive (3D printing) and subtractive (turning, milling) manufacturing processes. This approach allows manufacturers to build parts layer by layer and refine them using traditional machining techniques. Such a combination ensures rapid prototyping, customization, and enhanced precision in the final product.
Real-time Monitoring and Feedback
Integrating sensors and advanced monitoring systems in lathes and CNC machines will enable real-time feedback during the manufacturing process. This means that any deviations or errors can be instantly detected and corrected, ensuring consistent quality and reducing wastage.
Collaborative Robotics in Manufacturing
The rise of collaborative robots, or “cobots,” in manufacturing is hard to ignore. Unlike traditional robots that operate in isolation, cobots work alongside human operators. In turned parts manufacturing, cobots can handle repetitive tasks, assist in precision operations, and ensure that the human workforce can focus on complex, value-added activities. The synergy between humans and robots promises to elevate the efficiency and precision of the manufacturing process to unprecedented levels.
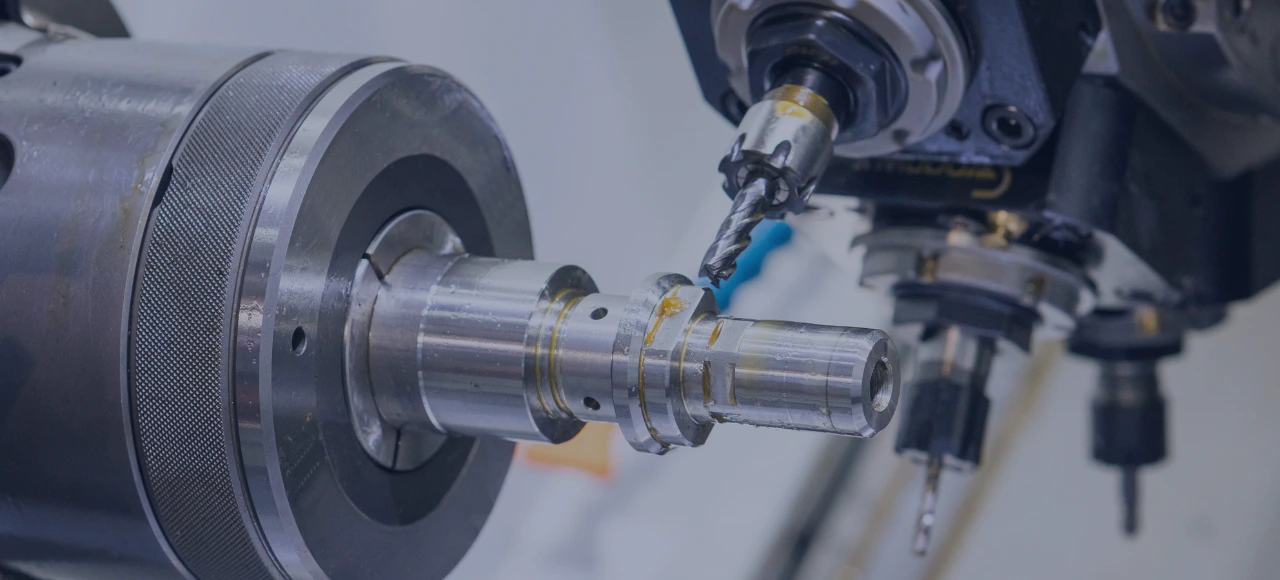
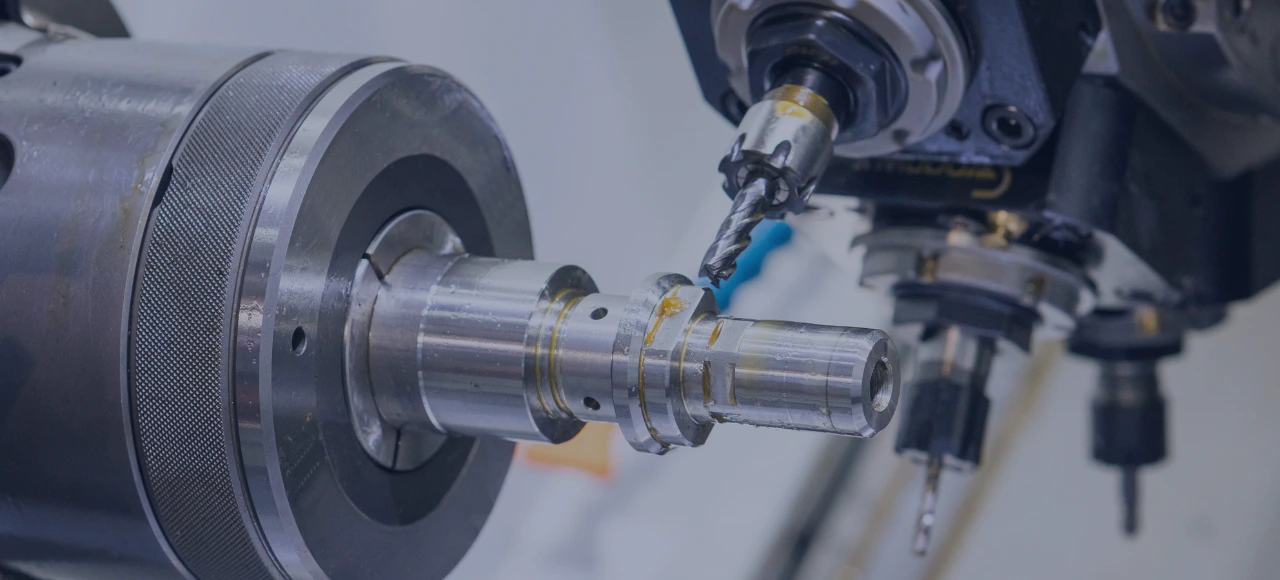
Integration of Artificial Intelligence and Machine Learning
The next frontier in component manufacturing is the integration of AI and machine learning. These technologies are not just buzzwords; they’re set to revolutionize how turned parts manufacturing operates.
Predictive Maintenance
With AI-driven algorithms, manufacturers can predict when a machine is likely to fail or when a tool needs replacement. This predictive maintenance ensures minimal downtime, as parts can be replaced or repaired before a breakdown occurs, leading to increased efficiency and reduced costs.
Quality Control and Assurance
The ML (Machine Learning) models can be trained to recognize defects or inconsistencies in manufactured parts. By analyzing thousands of images and data points, these models can detect even the slightest deviations from the desired specifications, ensuring that only top-quality components make it through the production line.
Process Optimization
AI can analyze amounts of data to determine the most efficient manufacturing processes. By evaluating variables like tool speed, material feed rate, and environmental conditions, AI can suggest optimizations that can improve production speed while maintaining or enhancing the quality of the turned parts.
Digital Twins in Manufacturing
It is a virtual representation of a physical product or process. In the context of turned parts manufacturing, digital twins can simulate the entire manufacturing process, from raw material to finished product. This virtual modeling allows manufacturers to:
- Test and Refine: Before actual production begins, different approaches and techniques can be tested in the virtual environment, ensuring optimal results in the real world.
- Monitor in Real-time: With sensors feeding data into the digital twin, manufacturers can monitor the production process in real-time, making adjustments as needed to ensure the best outcomes.
- Forecast and Plan: By analyzing data from the digital twin, manufacturers can forecast production needs, plan for maintenance, and ensure a smooth and efficient manufacturing process.
In The End
The detailed world of turned parts manufacturing is a testament to the marvels of modern engineering and technology. From its foundational methods to the latest innovations like AI, machine learning, and digital twins, this domain continues to evolve, offering unparalleled precision and efficiency.
Zetwerk is at the forefront of this evolution, ensuring that industries benefit from the best of what turned parts manufacturing offers. As we look to the future, it’s clear that the blend of traditional craftsmanship and cutting-edge technology will continue to shape industries, driving progress and setting new benchmarks in manufacturing excellence.




FAQS
Turned parts manufacturing is a specialized process where a workpiece is rotated and shaped using a cutting tool, primarily on a lathe machine, to produce intricate components.
Brass is favored in turned parts manufacturing due to its malleability and excellent conductivity, making it suitable for various applications.
CNC (Computer Numerical Control) turning uses computerized controls to operate the lathe, allowing for higher precision and the ability to create intricate designs compared to manual methods.
Multi-axis turning enables lathes to operate on multiple axes simultaneously, allowing for combined drilling, milling, and turning operations. This reduces the need for secondary processes, ensuring faster production and enhanced precision.
Cobots work alongside human operators in the manufacturing process. In turned parts manufacturing, they handle repetitive tasks, assist in precision operations, and allow humans to focus on more complex activities, enhancing efficiency and precision.