Introduction
Precision machining is an art that has revolutionized modern industries by enabling the production of complex and intricate parts with unparalleled accuracy. Achieved through computer numerical control (CNC) processes, precision machining involves the use of cutting-edge tools and machines to remove material from a workpiece, resulting in precise dimensions and tight tolerances. In this article, we delve into the world of precision machined components, exploring the various processes involved, their advantages, applications across industries, and suitable materials. By understanding the artistry behind precision machining, businesses can enhance their manufacturing capabilities and deliver high-quality products to meet customer demands.
Understanding Precision Machined Components
Precision machining is a subtractive manufacturing process that plays a vital role in creating intricate parts with high accuracy. It starts with a solid block or billet of material, such as metal or plastic, which is shaped using cutting tools to achieve tight tolerances and complex geometries. The process relies on advanced cutting tools and CNC machines to ensure precision at every step. Precision machining depends on below specifications.
- Cutting Tools
- CNC Machines
- Materials
- Steps in Precision Machining
Various Processes in Precision Machining
Precision machining encompasses a wide range of processes that contribute to achieving high accuracy and complexity in machined components. Let’s explore some of these processes:
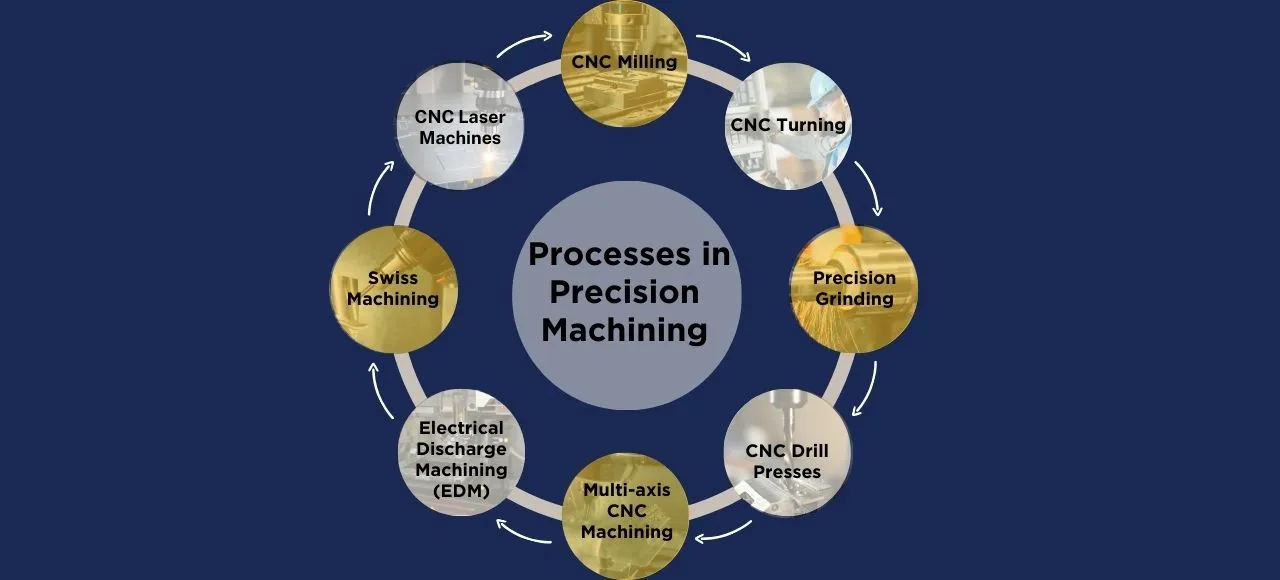
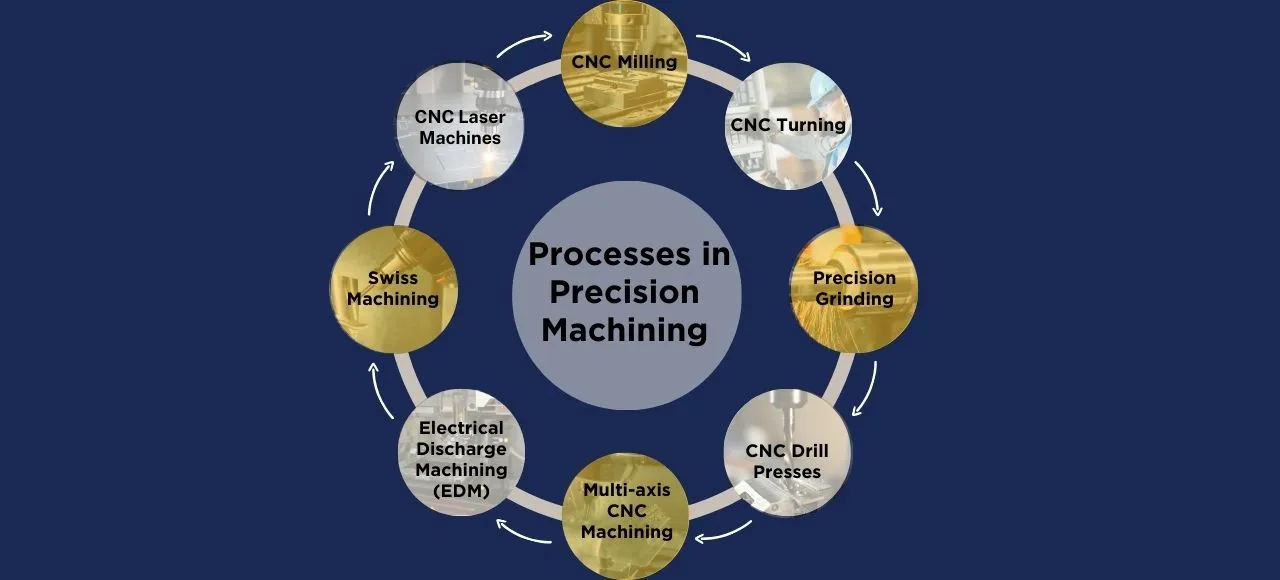
- CNC Milling: CNC milling uses rotary cutters to remove material from the workpiece in multiple axes simultaneously. It is suitable for creating complex shapes, pockets, slots, and features like chamfers and fillets. CNC milling allows for precise control over cutting speed, depth of cut, feed rate, and tool path.
- CNC Turning: CNC turning involves rotating the workpiece along a central axis while a linearly moving cutting tool removes excess material. This process is ideal for creating cylindrical shapes such as shafts or pins and can also be used to create features like threads or grooves on the workpiece.
- Precision Grinding: Precision grinding is employed to achieve tight tolerances and surface finishes on machined components. It uses abrasive wheels to remove material from the workpiece while ensuring precise dimensions.
- CNC Drill Presses: CNC drill presses are used to create holes of varying sizes and depths in precision machining. These machines provide accurate hole placement and can handle a variety of materials.
- Multi-axis CNC Machining: Multi-axis CNC machining combines various cutting tools and processes such as milling, waterjet cutting, or laser cutting to achieve complex part creation. These machines offer enhanced flexibility and are capable of producing intricate components with high precision.
- Electrical Discharge Machining (EDM): EDM is a process that uses electrical discharges between two electrodes to shape metal without physical contact. It is commonly used for machining hard metals and creating features like holes, slots, and tapers in gears.
- Swiss Machining: Swiss machining utilizes specialized Swiss-made CNC lathes with moving headstocks to provide precise and complex machining options. This process is particularly suitable for long and slender parts where tight tolerances are required.
- CNC Laser Machines: CNC laser machines employ high-frequency laser beams to slice or engrave materials accurately. They are versatile and can work on both metals and non-metals, making them suitable for a wide range of applications.
Advantages of Precision Machining
Precision machining offers several advantages that make it an indispensable process in modern manufacturing:
- Tight Tolerances: Precision machined components consistently meet strict dimensional tolerances, ensuring proper fitment and functionality in assemblies. Tight tolerances refer to the permissible variation from the desired dimensions and play a crucial role in industries such as aerospace, where accuracy is critical.
- High Accuracy: Precision machining achieves exceptional accuracy by following programmed instructions with negligible deviations. This ensures that parts match the original design blueprint precisely, resulting in reliable performance.
- High Repeatability: Every part produced through precision machining exhibits consistent quality due to high repeatability. Repeatability refers to the ability to reproduce identical parts repeatedly, reducing variations and maintaining uniformity across production batches.
- Reduced Production Costs: Precision machining minimizes defects during production through advanced automation techniques, resulting in cost savings. Automation reduces labor costs while improving efficiency by eliminating human errors that can lead to rework or scrap.
- Speed and Efficiency: Precision machining techniques enable high-speed production and efficient material removal, reducing cycle times. These processes utilize advanced robotics, high spindle speeds, and optimized tool paths to maximize productivity.
- Enhanced Safety: Precision machining techniques prioritize safety by minimizing the need for manual intervention. Operators are protected from potential hazards associated with traditional machining processes.
Applications of Precision Machined Components
Precision machined components find application in various industries that demand high-quality parts with tight tolerances and complex geometries. Some prominent examples include:
Automotive: The automotive industry relies on cnc machined components for engine parts, transmission systems, fuel injectors, braking systems, and suspension components. These components ensure smooth operation, durability, and efficiency of vehicles.
Aerospace: Aerospace applications require precision machined components for critical engine parts, turbine blades, landing gear mechanisms, control surfaces, and structural elements. These components must withstand extreme conditions while maintaining precision to ensure safe flight.
Medical: In the medical field, precision machined components are used in prosthetic limbs, surgical instruments, implants such as pacemakers or joint replacements, diagnostic equipment like MRI machines or CT scanners. Accurate dimensions and reliable performance are crucial to patient safety and optimal healthcare outcomes.
Defense: Precision machined components used in aerospace sector are used for weapon prototypes, missile guidance systems, armored vehicles’ critical parts or aircraft subsystems. Precision machining ensures accuracy and reliability in defense applications where lives depend on robust engineering.
Electronics: Precision machined components play a vital role in electronics manufacturing by producing microchips with intricate circuitry patterns. They also contribute to heat dissipation solutions like heat sinks or enclosures for electronic devices.
Energy: Power generation equipment requires precision machined components for turbines, generators’ rotor assemblies or gears used in wind energy systems or hydroelectric power plants. Accurate dimensions are crucial for optimal performance and efficiency of these systems.
If you’re looking for precision machined components, explore Zetwerk’s range of manufacturing services. With their expertise in precision machining and strict quality control measures, they deliver high-quality products for diverse industries. Visit the Zetwerk Knowledge Hub to learn more.




FAQs
Several factors influence the cost of precision machining, including complexity, material selection, volume, tolerances required, design revisions, finishing requirements, and additional services like assembly or testing.
Outsourcing precision machined parts is beneficial when a company lacks in-house capabilities or specialized equipment. It offers cost savings without compromising on quality while accessing advanced technology and expertise from experienced manufacturers.
While other processes like additive manufacturing (3D printing) can create complex parts, precision machining remains irreplaceable due to its ability to achieve tight tolerances, high accuracy, repeatability, and superior surface finishes necessary for critical applications.
Industries such as automotive, aerospace, medical devices, defense systems, electronics, and power generation rely heavily on precision machined components due to their need for reliable performance and compliance with stringent quality standards.
Precision component manufacturers employ various quality control measures such as ISO certifications, statistical process control techniques, dimensional inspections using coordinate measuring machines (CMM), and visual inspections at different stages of production to ensure exceptional accuracy and reliability.