Introduction
Rapid prototyping parts has become a game-changer in manufacturing, enabling businesses to bring their innovative ideas to life swiftly and efficiently. Prototype CNC (Computer Numerical Control) machining is at the forefront of this revolution, offering a powerful and precise method for creating prototypes of various products. This blog will delve into prototype CNC machining, exploring the process from design to production, its benefits, applications, and its role in transforming the manufacturing landscape.
Understanding Prototype CNC Machining
Prototype CNC machining is a manufacturing process that utilizes computer-controlled machines to cut and shape raw materials into a prototype or a small batch of parts. CNC machines follow instructions from computer programs to execute precise movements and produce complex parts with high accuracy and repeatability. This method has revolutionized traditional prototyping, enabling engineers and designers to test and refine their concepts before moving to full-scale production.
Prototype CNC Machining Process
- CNC Machining: The machine executes the programmed instructions, cutting and shaping the material according to the 3D model. The process is highly automated, requiring minimal manual intervention.
- Material Selection: The next step involves selecting the appropriate material for the prototype. Materials like metals (aluminum, steel, titanium), plastics (ABS, PVC, nylon), or composites can be used depending on the application.
- Testing and Iteration: The finished prototype is subjected to rigorous testing and evaluation to assess its performance and functionality. Feedback from testing is used to make necessary design improvements for subsequent iterations.
- Programming the CNC Machine: The CAD files are converted into machine-readable code using computer-aided manufacturing (CAM) software once the design and material selection are complete. This code contains instructions for the CNC machine to cut and shape the material precisely.
- Setup and Calibration: The CNC machine is calibrated to ensure it operates accurately and consistently. This includes securing the material on the machine’s work table and aligning the cutting tools.
- Finishing and Quality Control: The prototype is inspected for imperfections or inaccuracies once the CNC machining is complete. Finishing processes like sanding, polishing, or painting may be applied to achieve the desired surface quality.
- Finalization and Full-Scale Production: After multiple iterations and refinements, the final prototype design is approved for full-scale production. The prototype CNC machining process paves the way for efficient and reliable product mass production.
- Design Phase: The prototype CNC machining process begins with the design phase. Engineers and designers create detailed 3D models of the part using computer-aided design (CAD) software. The CAD files serve as the blueprint for the CNC machine during machining.
Benefits of Prototype CNC Machining
- Material Versatility: Prototype CNC machining supports a wide range of materials, including metals, plastics, and composites, offering flexibility in material selection for different applications.
- Precision and Accuracy: CNC machines offer unparalleled precision and accuracy, ensuring the prototypes are manufactured to specifications.
- Design Validation: Prototypes created through CNC machining allow designers to validate their designs, identify potential issues, and make necessary improvements early in development.
- Complex Geometries: CNC machining allows the creation of intricate and complex geometries that may be challenging or impossible to achieve using traditional manufacturing methods.
- Cost-Effectiveness: Producing prototypes using CNC machining is cost-effective, especially compared to traditional tooling methods, which can be expensive and time-consuming.
- Speed and Efficiency: Prototype CNC machining enables rapid production of prototypes, significantly reducing the time between design iterations and finalizing a product design.
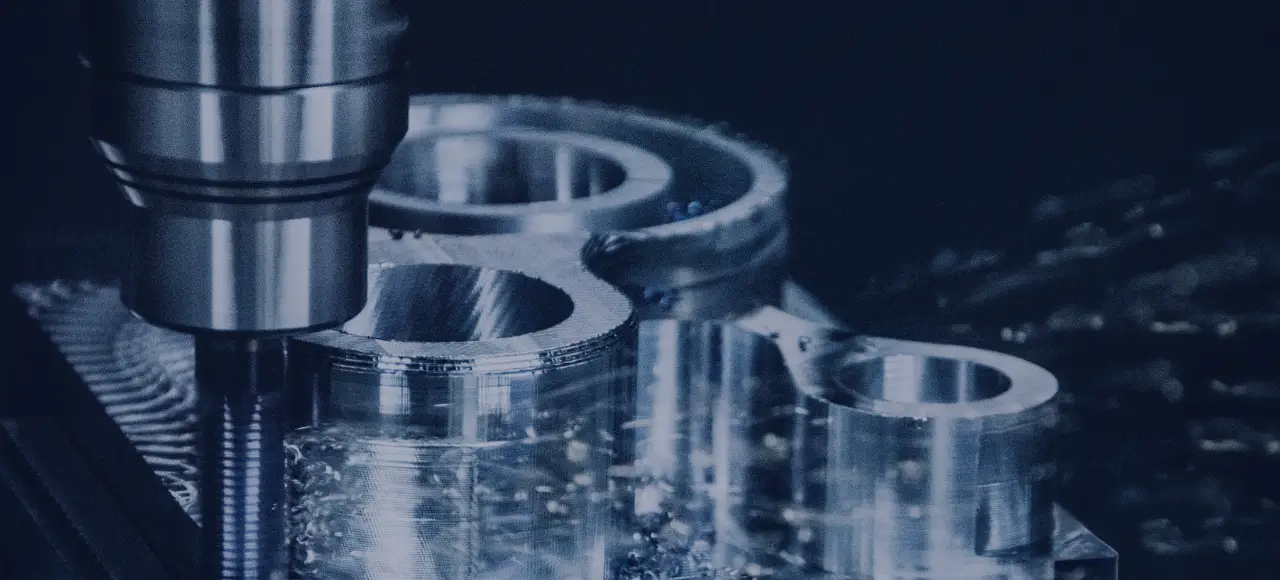
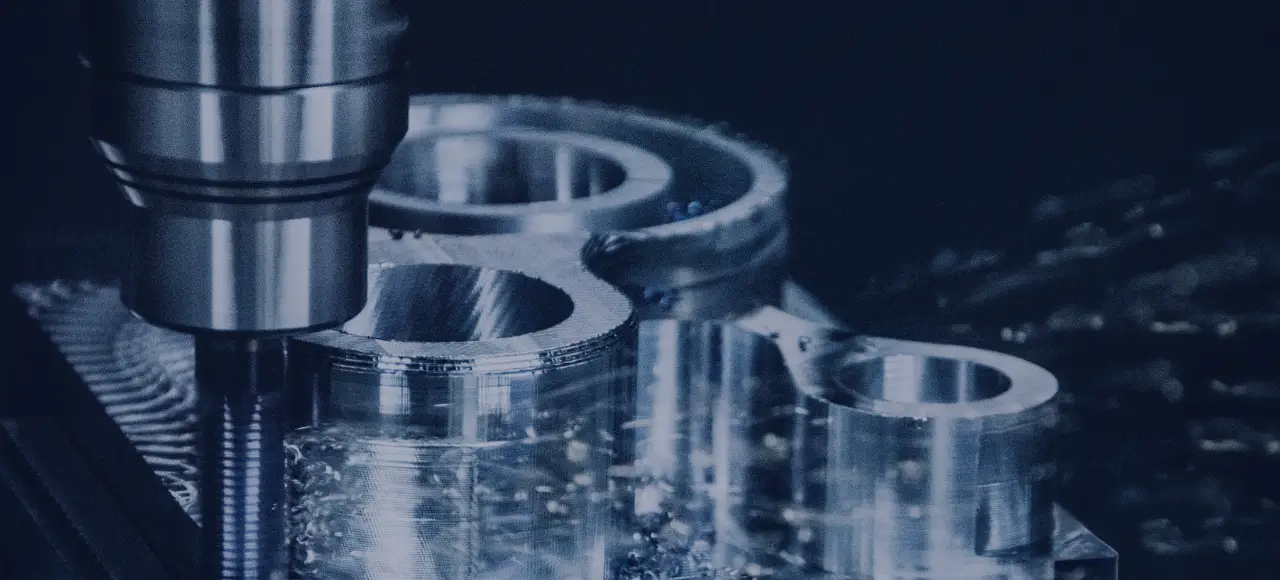
Applications of Prototype CNC Machining
- Medical Device Prototyping: The medical industry uses prototype CNC machining to create and test medical devices, prosthetics, and implants.
- Architectural Modeling: CNC machining creates detailed architectural models and prototypes in architecture and construction.
- Product Development: Prototype CNC machining is extensively used in product development across various industries, including automotive, aerospace, electronics, and consumer goods.
- Customization: Prototype CNC machining facilitates the production of custom parts and components, catering to unique and specific requirements.
- Jewelry Prototyping: The jewelry industry uses CNC machining to create intricate and precise prototypes for custom jewelry designs.
Challenges in Prototype CNC Machining
- Design Complexity: While CNC machines can handle complex designs, incredibly intricate geometries may pose challenges regarding machining time and cost.
- Material Selection: Choosing a suitable material for the prototype is critical to ensure that the final product meets the desired specifications and performance requirements.
- Post-processing: Some prototypes may require additional post-processing, such as surface finishing, to achieve the desired appearance and texture.
- Quality Control: Ensuring the quality and accuracy of the final prototype requires meticulous inspection and testing processes.
To Summarize
Prototype CNC machining has revolutionized how products are developed and brought to market. This manufacturing process empowers engineers, designers, and businesses to iterate and refine their designs efficiently by providing a swift and precise method for creating prototypes. The benefits of speed, accuracy, and material versatility make prototype CNC machining a vital tool in various industries, from automotive and aerospace to medical and consumer goods. As technology advances, the role of prototype CNC machining in transforming the manufacturing landscape is set to grow, paving the way for future innovative and groundbreaking products.




FAQs
Prototype CNC machining is a manufacturing process that utilizes computer-controlled machines to create precise prototypes of products from 3D CAD models. It involves cutting and shaping raw materials to bring the design to life for testing and validation.
Prototype CNC machining supports many materials, including metals (such as aluminum, steel, and titanium), plastics (like ABS, PVC, and nylon), composites, and exotic materials.
CNC machining offers high precision, with tolerances typically ranging from 0.1 mm
to 0.02 mm, depending on the material and machine capabilities.
CNC machining is a subtractive manufacturing process that removes material from a block or sheet, while 3D printing is an additive process that builds layers to create the final object. CNC machining is suitable for producing high-precision and functional prototypes, whereas 3D printing is better for rapid prototyping and complex geometries.
Yes, CNC machining is often cost-effective for small production runs, especially
compared to traditional tooling methods that require expensive molds or dies.