Medical machined components are essential in the healthcare industry. They are the foundation of medical devices and equipment crucial for patient care, diagnosis, and treatment. These components are used in surgical instruments and medical imaging equipment, and their precision is vital to the safety and effectiveness of medical procedures. Every detail matters, making these components essential for the healthcare ecosystem.
However, the manufacturing of medical machined components has its complexities. It requires a unique blend of engineering expertise, material knowledge, and adherence to stringent quality standards. Additionally, navigating the ever-evolving medical regulations and standards requires meticulous attention to detail. Let’s explore the complexities of medical machined components and how technology plays a considerable role in precision and quality.
The Significance of Medical Machined Components
Precision Beyond Measure
In many medical applications, even the slightest deviation can have life-altering consequences. Precision is the hallmark of medical component manufacturing, from intricate surgical instruments to implantable devices.
Materials Matter
The selection of materials for medical component manufacturing is crucial. Biocompatible materials, which are safe for implantation within the human body, are often necessary. Additionally, these materials must withstand sterilization and repeated use without degrading.
Regulatory Compliance
The medical industry is heavily regulated, and compliance with standards such as ISO 13485 and FDA requirements is non-negotiable. Manufacturers of medical machined components must adhere to strict quality control processes to ensure compliance and patient safety.
Customization for Unique Applications
Medical devices and equipment often require custom components tailored to specific applications. Whether it’s a specialized surgical instrument or a component for an imaging system, customization is the norm in medical manufacturing.
Challenges in Medical Component Manufacturing
The production of medical machined components is not without its challenges:
- Complexity of Design: Many medical components have highly complex and intricate designs. Manufacturing these components requires advanced machining techniques and equipment.
- Material Selection: Choosing the right materials for medical components can be challenging due to the need for biocompatibility, corrosion resistance, and other specific properties.
- Quality Control: Uncompromising quality control measures are essential to ensure that every component meets the required standards. This includes thorough testing and inspection processes.
- Regulatory Hurdles: Navigating the regulatory landscape in the medical industry can be daunting. Manufacturers must stay up-to-date with evolving regulations and ensure compliance at all times.
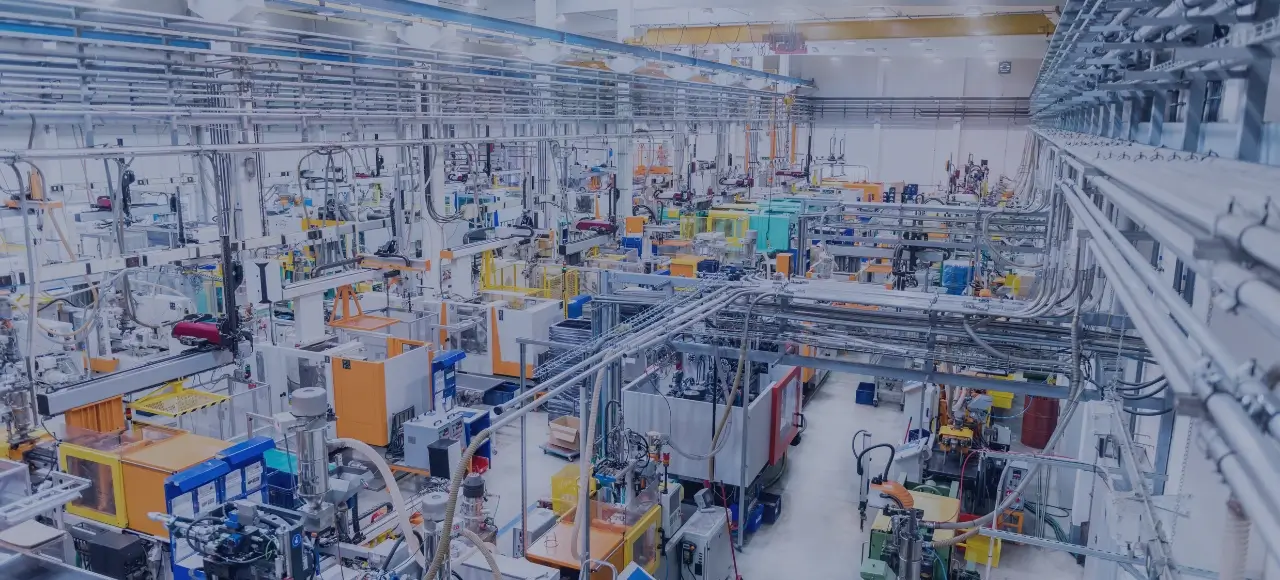
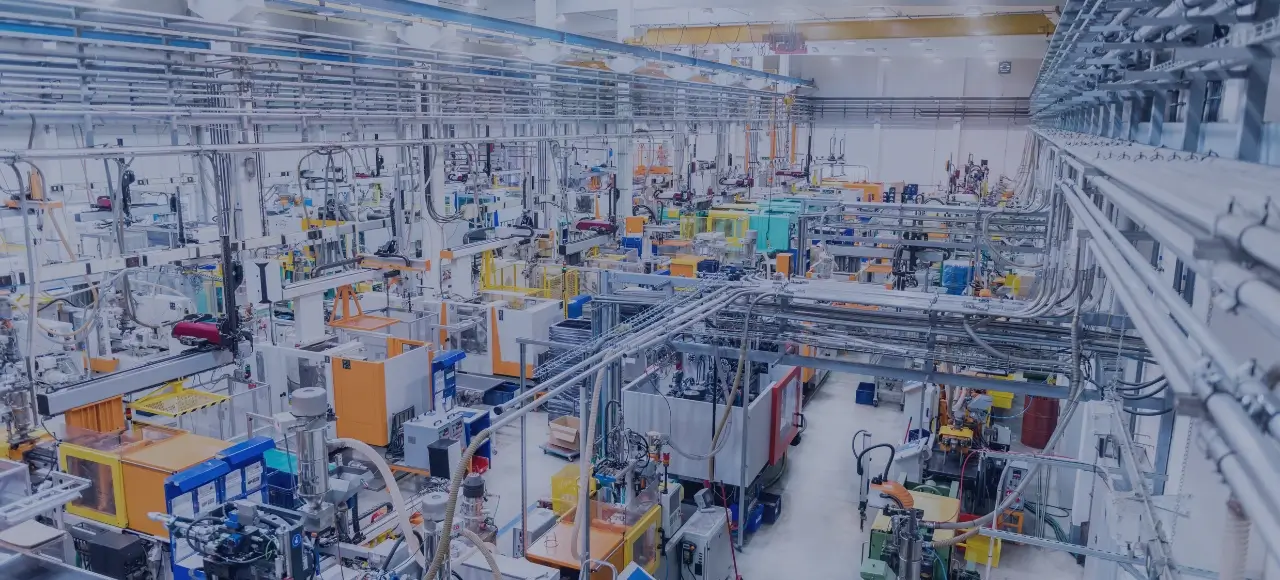
Advancements in Modern Technologies: Advancing Precision and Quality in Medical Machined Components
When it comes to medical machined components, precision and quality are essential. These components are integral to medical devices and equipment; even the slightest deviation can have serious consequences. Fortunately, modern technologies have revolutionized the manufacturing process of medical components, resulting in higher levels of precision and quality. Let’s explore how these advancements have transformed the industry.
Computer-Aided Design (CAD) and Computer-Aided Manufacturing (CAM)
Modern CAD and CAM software have revolutionized the design and manufacturing of medical components. Engineers can now create highly intricate and precise component designs, considering even the most complex geometries. These digital designs seamlessly translate into manufacturing instructions for advanced CNC machining processes. The result is components that meet exacting specifications with unprecedented precision.
High-Precision CNC Machining
The advent of high-precision CNC machining (Computer Numerical Control) has been a game-changer for medical component manufacturing. These machines are capable of ultra-precise operations, with tolerances measured in micrometers. CNC machining ensures that every cut, groove, and contour adheres meticulously to the design, resulting in components that exhibit exceptional precision.
Advanced Materials
Developing advanced materials explicitly engineered for medical applications has significantly enhanced precision and quality. These materials possess attributes such as biocompatibility, corrosion resistance, and stabilizability. They meet the stringent requirements of medical component manufacturing and provide the durability and reliability needed for critical medical devices.
Additive Manufacturing (3D Printing)
Commonly known as 3D Printing, Additive Manufacturing has expanded the horizons of design and precision. It allows for the creating of complex, customized, and patient-specific components that were previously challenging to produce. 3D Printing’s layer-by-layer approach enables incorporating intricate features, reducing the need for post-processing and enhancing overall quality.
Robotics and Automation
The use of robotic systems and automation has greatly enhanced the consistency and repeatability of manufacturing processes. Robots are capable of performing tasks that are difficult to accomplish manually, with an unparalleled level of precision and consistency. The implementation of automation also significantly minimizes the risk of human error, guaranteeing that each component meets the same high-quality standards.
Advanced Quality Control
Technological advancements in quality control and inspection have raised the bar for medical component quality. Automated inspection systems use cutting-edge imaging and measurement technologies to detect the slightest deviations from specifications. This level of precision in inspection ensures that every component is of the highest quality.
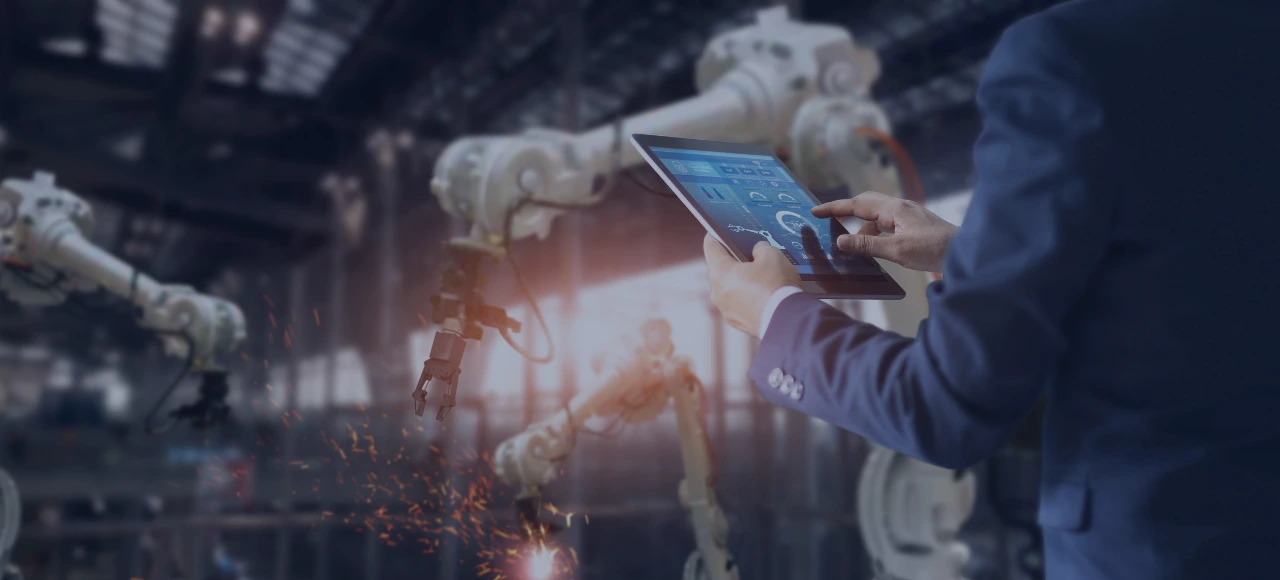
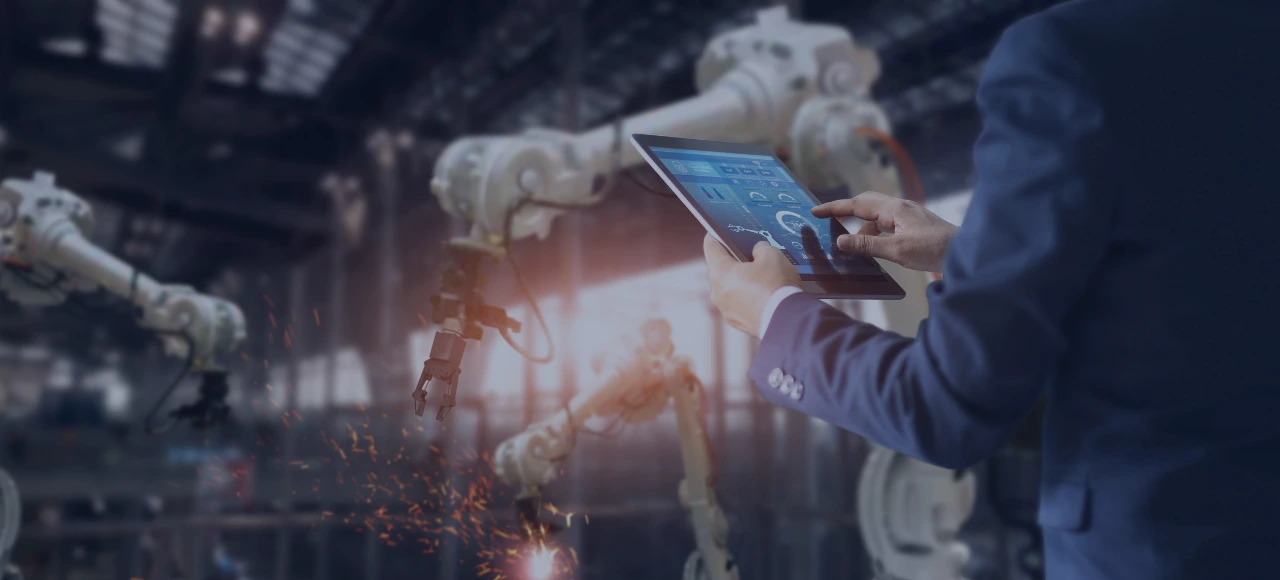
Machined Medical Components and Applications
CNC Turned Medical Components:
- Surgical Instrument Shafts: Precision cylindrical components used in surgical tools.
- Dental Implant Abutments: Customized components for dental applications.
- Prosthetic Limb Components: Precision components for artificial limbs.
CNC Milled Medical Components:
- Medical Device Housings: Enclosures for housing electronic medical devices.
- Orthopedic Implant Plates: Precision plates used in orthopedic surgeries.
- MRI Components: Precision components for magnetic resonance imaging systems.
CNC Drilled Medical Components:
- Medical Screws: Threaded fasteners used in orthopedic and dental applications.
- Medical Pins: Cylindrical components with various end configurations.
- Medical Needles: Precision needles for different medical procedures.
CNC Ground Medical Components:
- Precision Rollers: High-precision cylindrical rollers used in medical equipment.
- Medical Tool Inserts: Inserts for medical cutting and drilling tools.
- Medical Valve Components: Components for controlling fluid flow in medical devices.
EDM Machined Medical Components:
- Medical Mold Inserts: Precision inserts for molding medical device components.
- Implantable Medical Components: High-precision components used in implants.
- Catheter Components: Intricate components for medical catheters.
Laser-Cut Medical Components:
- Surgical Blades: Precision-cut blades used in various surgical procedures.
- Stents: Intricate components used in vascular and cardiac applications.
- Medical Brackets: Support components used in medical equipment.
Zetwerk – Your Partner in Precision Healthcare
In medical machined components, precision is not just a requirement; it’s a necessity. With Zetwerk as your partner, you can confidently navigate the complex landscape of medical component manufacturing Zetwerk’s expertise, commitment to quality, and dedication to innovation make it the ideal partner for healthcare professionals and organizations looking to make a difference in patient care.




FAQs
Medical machined components are precision-engineered parts used in medical devices and equipment. They are crucial in healthcare as they contribute to the reliability and functionality of medical instruments and appliances. Their precision ensures accurate diagnosis, treatment, and patient care.
Medical machined components are typically made from biocompatible, corrosion-resistant materials capable of withstanding sterilization processes. Common materials include stainless steel, titanium, aluminum, and medical-grade plastics.
Precision in medical component manufacturing is achieved through advanced machining techniques, including CNC machining. Computer-aided design (CAD) and computer-aided manufacturing (CAM) software are crucial in creating precise component designs, which are then translated into manufacturing instructions for CNC machines.
Medical machined components must adhere to stringent regulatory standards, such as ISO 13485 and FDA requirements. These standards ensure that the parts meet strict quality and safety criteria and are suitable for use in medical devices.
A reliable manufacturing partner with expertise in medical component manufacturing can provide valuable support in design, material selection, quality control, and compliance with regulations. They can also offer customization to meet specific medical device requirements, ensuring that components are of the highest quality and precision.