Aluminum extrusion profiles are widely used in various industries due to their versatility, lightweight nature, and excellent strength-to-weight ratio. These custom profiles are manufactured through a precise process that involves shaping aluminum into complex cross-sectional shapes. This article delves into the complete process of manufacturing custom aluminum extrusion profiles, providing valuable insights into the techniques and steps involved.
What Are Custom Aluminum Extrusion Profiles?
Custom aluminum extrusion profiles are versatile and essential components used in various industries. These profiles are created through a precise manufacturing process that involves shaping aluminum into specific cross-sectional shapes. With their lightweight nature and excellent strength-to-weight ratio, custom aluminum extrusion profiles offer numerous advantages.
They can be tailored to meet specific project requirements and find applications in construction, automotive, aerospace, and more. By understanding the manufacturing process and exploring trusted suppliers like Zetwerk, businesses can leverage the benefits of custom aluminum extrusion profiles for their projects.
Step-by-Step Guide to Manufacturing Aluminum Extrusion Profiles
Aluminum extrusion is a versatile and widely used process for creating intricate profiles used in various industries. Follow these steps to manufacture aluminum extrusion profiles:
Step 1: Aluminum alloy selection
Aluminum alloy selection is the vital first step in crafting precise extrusion profiles. Choosing the right alloy dictates the profile’s strength, corrosion resistance, and other characteristics. This decision forms the foundation for a successful extrusion process, ensuring the final product meets design requirements and performance expectations.
Step 2: Custom Extrusion Design and Die Preparation
Begin by designing the desired shape and dimensions of the aluminum extrusion profile using specialized software. Once the design is finalized, create a die, which is a tool that shapes the aluminum under pressure. The die should match the profile’s specifications and intricacies.
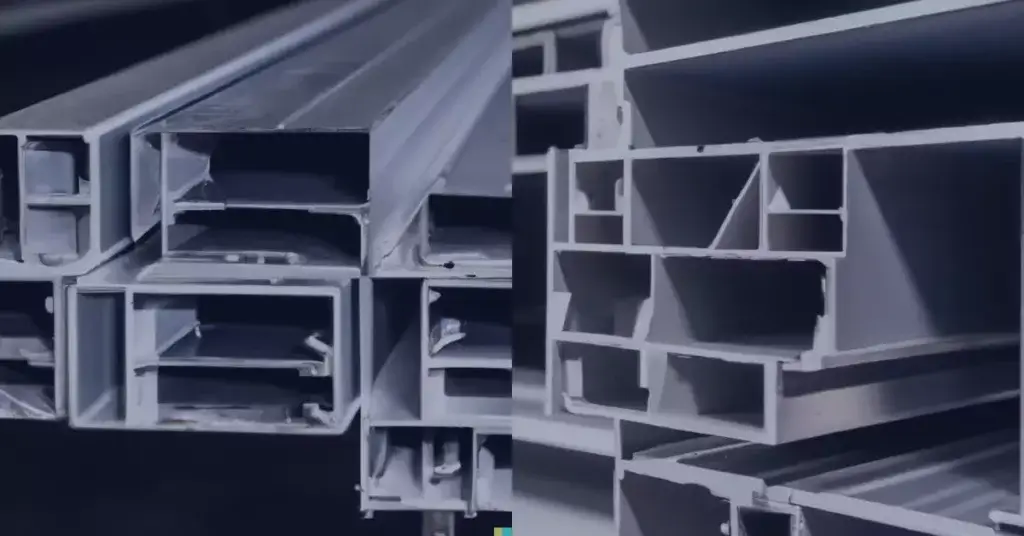
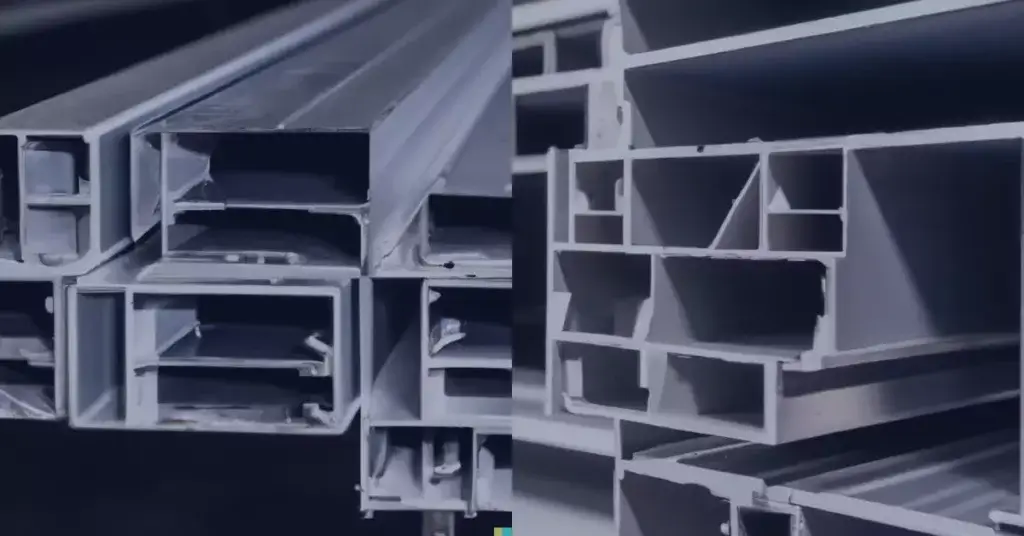
Step 3: Billet Heating
Load an aluminum billet, a cylindrical piece of aluminum, into a furnace and heat it to the required temperature. Heating makes the aluminum malleable and ready for extrusion.
Step 4: Extrusion Tooling Process
The heated billet is pushed through the die using a hydraulic press. The pressure forces the aluminum to take on the shape of the die’s opening. As the aluminum passes through, it forms the desired profile.
Step 5: Cooling and Cutting
After extrusion, the newly shaped aluminum profile is rapidly cooled using water or air to maintain its structural integrity. Once cooled, the continuous extrusion is cut into desired lengths using a saw or other cutting tools.
Step 6: Straightening and Quality Check
The extruded profiles may undergo a straightening process to correct any distortions caused during extrusion. Finally, conduct a quality check to ensure that the dimensions, surface finish, and overall quality meet the required standards.
Step 7: Packaging and Distribution
Approved profiles are packaged securely to prevent damage during transportation. They are then distributed to manufacturers for use in various applications.
Manufacturing aluminum extrusion profiles involves precision, technology, and expertise. Following these steps ensures the creation of high-quality profiles that serve diverse industries effectively.
Secondary Operations Involved In Manufacturing Custom Aluminum Extrusion Profiles
Secondary operations play a crucial role in the manufacturing process of custom aluminum extrusion profiles. These operations are performed after the extrusion process to further refine and enhance the profiles, ensuring they meet specific project requirements. Let’s explore some common secondary operations involved in the production of custom aluminum extrusion profiles:
- Cutting and Sawing
Once the extrusion process is complete, the profiles are cut to the desired lengths using precision saws. This step ensures that the profiles are accurately sized and ready for further processing.
- Machining
Machining operations involve drilling, milling, and tapping to create holes, threads, or other intricate features in the profiles. This process adds functionality and allows for easy integration of the profiles into larger assemblies.
- Surface Treatment
Surface treatment options like anodizing, powder coating, or painting are applied to enhance the appearance, durability, and corrosion resistance of the profiles. These treatments also provide opportunities for branding and customization.
- Precision Cutting and Mitering
Profiles may undergo precision cutting and mitering to achieve specific angles or shapes required for assembly. This operation ensures seamless and accurate connections between profiles during installation.
These secondary operations add value to the custom aluminum extrusion profiles by expanding their functionality, improving aesthetics, and meeting specific project requirements. By leveraging these processes, manufacturers can deliver profiles that precisely match the desired specifications of their customers.
Enhance Your Projects with Zetwerk Aluminum Extrusion Profiles
Manufacturing custom aluminum extrusion profiles involves a meticulous process that combines design, heating, extrusion, cooling, finishing, and fabrication. Each step is crucial to ensuring the creation of high-quality profiles that meet precise specifications. By understanding this complete process, buyers can make informed decisions when sourcing aluminum extrusion profiles for their projects.
Zetwerk offers a wide range of custom aluminum extrusion profiles through its trusted network of verified suppliers. With their precision machining and fabrication expertise, Zetwerk provides seamless end-to-end solutions for your manufacturing needs. Explore Zetwerk capabilities in aluminum extrusions and discover how their services can benefit your business. Explore aluminum extrusions on Zetwerk for more information.




FAQs
The manufacturing time for custom aluminum extrusion profiles depends on various factors such as complexity, quantity, and finishing requirements. It typically ranges from a few days to a few weeks.
Custom aluminum extrusion profiles find applications in the construction, automotive, aerospace, electronics, and renewable energy industries. They are utilized in producing windows, doors, frames, heat sinks, enclosures, and structural components.
Yes, aluminum is highly recyclable. Custom aluminum extrusion profiles can be recycled and reused, making them an environmentally friendly choice.
Aluminum extrusion profiles offer several advantages, including lightweight construction, excellent strength-to-weight ratio, corrosion resistance, thermal conductivity, and design flexibility. They can be tailored to meet specific project requirements.
Custom aluminum extrusion profiles offer significant design possibilities due to their versatile nature. However, complex designs may require additional considerations during the manufacturing process. Collaborating with experienced suppliers, like Zetwerk, can help overcome design challenges and ensure successful production.