Extruded Heat Sinks
Extruded heat sinks are cooling devices manufactured through an extrusion process, which involves shaping a heated material by forcing it through a die. A well-designed heat sink increases the surface area available for heat transfer, which allows for more efficient dissipation. This principle is central to the effectiveness of extruded heat sinks.
Here are the key steps and factors to consider when designing and manufacturing an extruded heat sink:-
Design considerations
- Geometry and dimensions: The shape and dimensions of the heat sink are crucial. Common shapes include finned, pin, and plate-type heat sinks. The design should consider the available space, airflow conditions, and the heat source’s characteristics. Factors to consider include base thickness, fin height, fin spacing, and overall dimensions.
- Fin configuration: The arrangement of fins on the heat sink majorly affects its thermal performance. Fins increase the surface area for heat dissipation. Factors to consider include fin density (number of fins per unit length), fin shape (rectangular, triangular, trapezoidal), and fin thickness.
- Thermal interface material (TIM): The material used between the heat sink and the component (e.g., thermal paste or pad) is crucial for reducing thermal resistance at the interface. Proper application and uniform thickness of TIM are essential.
- Base thickness: The base thickness of the heat sink is crucial as it determines the contact area with the heat source. Thicker bases offer better heat spreading, but trade-offs in weight and cost must be considered.
- Mounting method: Heat sinks can be attached to components using various methods, including clips, adhesives, or screws. The mounting mechanism impacts the ease of assembly, stability, and the overall thermal pathway.
- Airflow considerations: Heat sinks rely on natural or forced convection to dissipate heat. Designing the heat sink to optimize airflow around the fins enhances its cooling capacity. In some cases, heat sinks are paired with fans for increased efficiency.
Manufacturing processes
- Billet preparation: The chosen material (usually aluminum) is cast into billets of specific dimensions. These billets are heated to a suitable temperature for extrusion
- Billet conditioning: Billets may undergo homogenization treatment to ensure uniform material properties and reduce internal stresses.
- Extrusion ratio: The ratio of the cross-sectional area of the die to the area of the extruded aluminium impacts the material’s flow characteristics and the final heat sink’s dimensions.
- Extrusion: The heated billet is pushed through a specially designed die using a hydraulic press. The die imparts the desired cross-sectional shape, including the fins and base, to the extruded heat sink.
- Quenching: Heat sinks may be quenched after extrusion to lock in desired material properties and prevent further cooling-induced changes.
- Cutting and finishing: Once the extruded profile has cooled and solidified, it is cut into individual heat sinks of the required length. Further finishing processes, such as CNC machining or surface treatments, may be applied to meet specific design criteria.
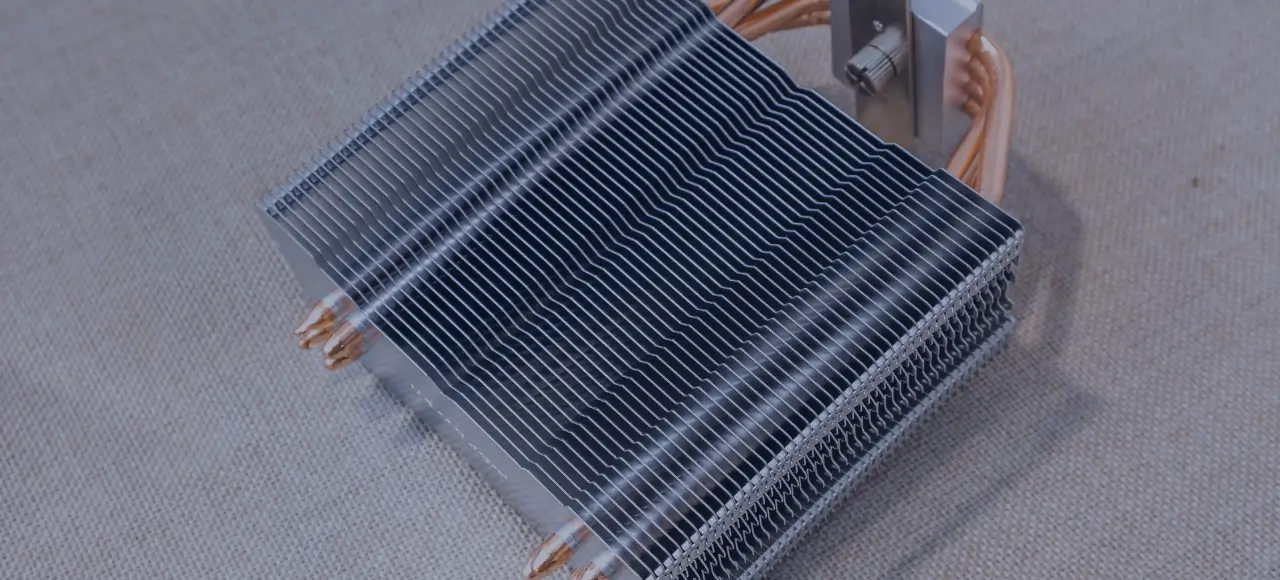
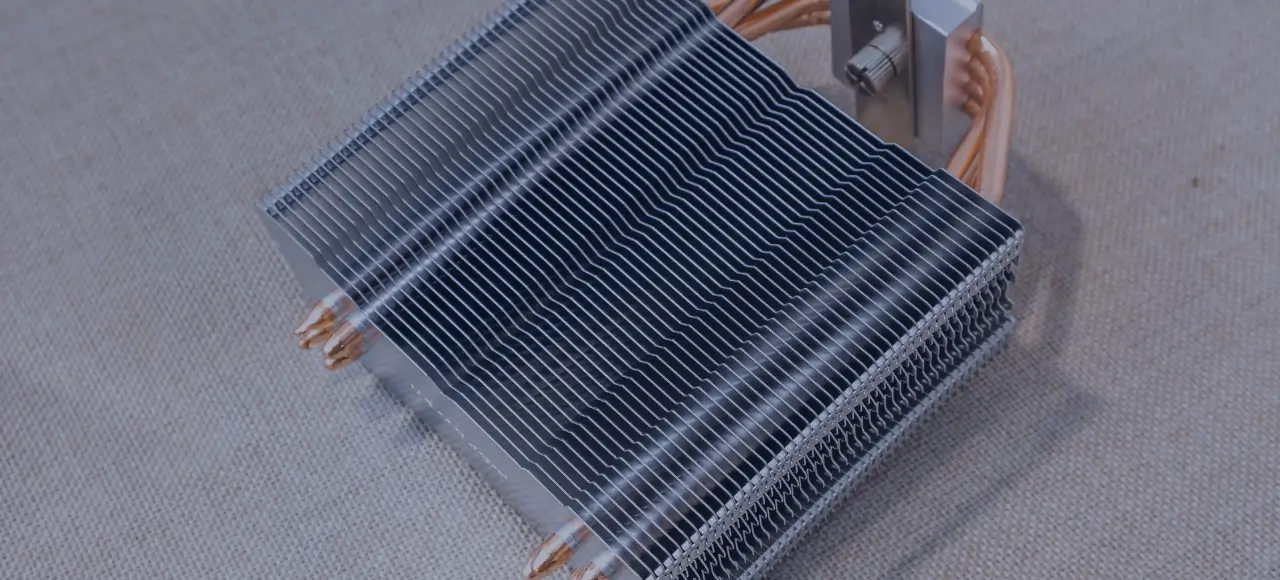
Applications of Extruded Heat Sinks
- Electronics: In the realm of electronics, extruded heat sinks are found in computers, laptops, servers, and telecommunication equipment. They are essential for cooling CPUs, GPUs, voltage regulators, and other power-intensive components.
- LED Lighting: LEDs generate heat during operation, which can degrade their performance and lifespan. Extruded heat sinks effectively manage this heat, allowing LEDs to maintain their brightness and efficiency over time.
- Automotive: electronic components. Extruded heat sinks play a crucial role in cooling power electronics in electric and hybrid vehicles, as well as in traditional internal combustion engine systems.
- Industrial Equipment: Many industrial machines and manufacturing processes generate significant amounts of heat. Extruded heat sinks are used to maintain the optimal operating temperature of motor drives, power supplies, and automation equipment.
- Renewable Energy: Solar inverters and wind turbine controllers require efficient heat dissipation for uninterrupted performance. Extruded heat sinks aid in managing the heat generated by power conversion processes in these systems.
- Consumer Electronics: From gaming consoles to audio amplifiers, consumer electronics benefit from the thermal management provided by extruded heat sinks. They prevent overheating and ensure consistent performance.
Extruded heat sinks are vital for managing heat in today’s technology landscape. Their intricate designs and efficient production methods make them essential for optimal device performance. Zetwerk, a key player in manufacturing, has been at the forefront of advancing extruded heat sink technology. By combining advanced techniques with tailored solutions, Zetwerk has elevated heat sink capabilities across industries.




FAQs
The aspect ratio, which is the ratio of fin height to fin thickness, affects the heat sink’s ability to dissipate heat. Lower aspect ratios improve heat transfer at the cost of increased pressure drop, while higher aspect ratios are more efficient for laminar airflow conditions.
Materials like graphite composites and synthetic diamonds have been explored for their high thermal conductivity. While they offer excellent heat transfer properties, their cost and manufacturability often limit their practical use in heat sinks.
Yes, advancements in surface treatments like anodizing, electroless nickel plating, or applying thin coatings can improve heat sink performance by enhancing thermal emissivity, corrosion resistance, and overall heat transfer efficiency.
Yes, heat pipes can be integrated into extruded heat sinks to enhance their cooling capabilities. Heat pipes transfer heat more efficiently than solid materials, allowing for better distribution and dissipation.
Vertical orientation may take advantage of natural convection, while horizontal orientation might benefit from forced convection due to better airflow. The application and ambient conditions dictate the optimal orientation.