With so many benefits of aluminum extrusion profiles, heat sinks are a great result of extrusion that eliminates high-temperature challenges in various industrial applications. From residential devices, and commercial systems, to aerospace parts, aluminum heat sinks are found in almost every device. Every electrical equipment that generates heat during power supply needs heat sinks that help for cooling purposes.
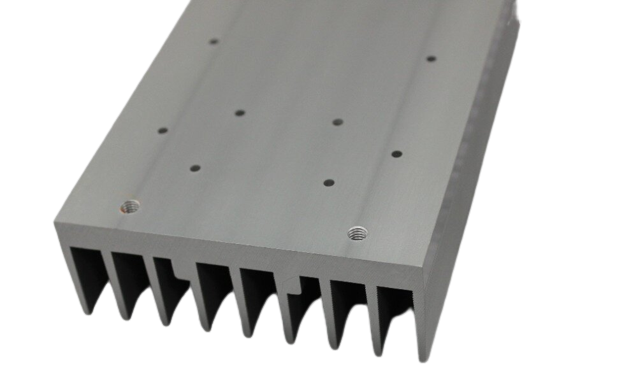
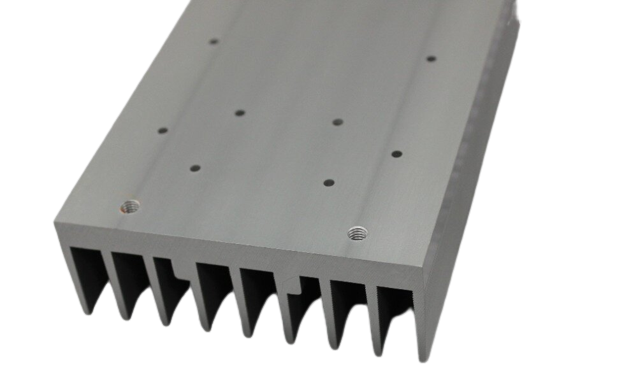
Heat sinks are a type of passive heat resistant that run to regulate the heat or temperature of mechanical and electronic equipment and small devices. They transfer the heat from a heat-generating component to either air or liquid coolant, enabling the device to work properly without overheating.
The incredible heat-resistant quality of aluminum makes heat sinks used in a wide range of industries. Also, creating heat sinks with aluminum is easier due to its variations as compared to other metals like copper.
ADVANTAGES OF ALUMINUM HEAT SINK EXTRUSION
While the main function of a heat sink is to regulate temperature and prevent any heating issues, it also aids in preventing breakage and even provides heat in case the temperature is too low. Aluminum and copper in heat sinks are the two primary metals used in creating heat sinks.
Here are some of the benefits of extruded aluminum heat sinks:
- Aluminum is a great thermal conductor, which is the main factor while creating heat sinks. In addition to this, it is popular for heat dissipation, high-strength metal heating, and lightweight material. The metal can be squeezed into various shapes of radiation, whether its wide flat heat sinks or oval sinks.
- The Corrosion-resistant and rust-free material of aluminum is another reason why aluminum extrusion heatsinks are widely used across industries as it serves along without causing any heating issues.
Apart from all these, aluminum is known for its energy-saving, simple maintenance, and low-cost use. Hence, most companies prefer custom aluminum extrusions for their manufacturing needs.
- High-pressure bearing and strength are among the qualities of aluminum extruded products. Even in the case of thinness or thickness, aluminum can handle sufficient pressure without getting damaged.
- Aluminum is capable to handle various surface treatments with a wide range of designs and colors, making the final product look durable and attractive to be used for different devices.






TYPES OF HEAT SINKS
Keeping the requirements in mind, heat sinks are widely used to create cooling equipment, here are the different types of aluminum heat sinks:
Stamped Heat Sinks
Stamped heat sinks are used for low-power devices and are low at cost. Made of metals that are stamped to create a particular shape these sinks are usually low in performance.
Folded Fin Heat Sinks
Folded fin heat sinks contain large surfaces and folded heat sink material. With high-performing quality, these are expensive as the cost of manufacturing is higher than other types of heat sinks.
Machining Heat Sinks
Expensive and high in performance, machining heat sinks are created with a gang saw for removing a section of material, to make inter fins with preset space.
Pin-fin Heat Sink
These sinks have pins at the base and are great in low airflow circumstances. The shape could be elliptical, square, or cylindrical.
Extruded Heat Sinks
The most popular and efficient type of heat sink is extruded heat sinks mainly created with aluminum. Available at a low cost with custom aluminum extrusion methods, the performance depends on the device and requirement.
More Types of Heat Sinks
- Forged Heat Sinks
- Skived Heat Sinks
- CNC Machines Heat Sinks
- Bonded Heat Sink






Heat Sink Applications
Here are the most common applications of heat sinks
- Microprocessor Cooling system, CPU, and devices.
- Solar thermal water plants
- Electrical devices
- Variable speed motor control
- Motor housing cooling
- Transaction drives
- Telecommunication drives
- Gas water heaters
- Industrial equipment
HOW ALUMINUM HEAT SINKS ARE CREATED?
Aluminum extrusion heat sinks are made from aluminum alloys ranging from 1050, 6060, and 6061, depending on thermal conductivity and strength, Most of the heat sinks are made of aluminum as it is affordable and lightweight. Using aluminum allows the process of refining, smelting, and scrapping to be pounded into foil, sheets, and fins, which are used in heat sinks.
Extrusion
Aluminum extrusion is done through aluminum billet under specific temperatures and using dies to create aluminum extrusion profiles, frames, and shapes. During the same process, heat sinks are designed for electrical cooling needs. Hot metal billets are forced through steel dues using aluminum 1050 and then anodized before the final shipping. The entire method is economic and effective for most devices.
Casting
In this method, the metal is poured into a mold. The pressure dies process to cast heat sinks is done to maintain a high level of mechanical properties. Casting is mostly done for zinc-cast heat sinks.
Skiving
Skiving is the process of cutting the metal into portions/slices. It is a common fabrication method for creating plate-fin and flared fin heat sinks. The procedure enables closely packed fins than in the extrusion process. It also provides a level or surface thickness, which slightly increases the total surface area.
Milling
An affordable way to create heat sinks from aluminum alloys. Also known as machined heating sinks, this is the process of cutting the material virtually with geometrical shapes.






With the advancement of technology and robotic automation, the manufacturing industry is changing rapidly. Today, complex-designed aluminum heat sinks are manufactured in no time. The varied use of heat sinks has made them usable across different industries.